産業用マーキングお役立ちコラム
産業用マーキング
お役立ちコラム
お役立ちコラム
「産業用マーキング」で業務改善ができることを聞いたことありますか?
企業での活用事例や、普段の業務の中で知っておくと得する情報をコラムにしています。
企業での活用事例や、普段の業務の中で知っておくと得する情報をコラムにしています。
関連キーワード一覧
インキ
スタンプ
記事数:16件 /更新日:2024.04.15
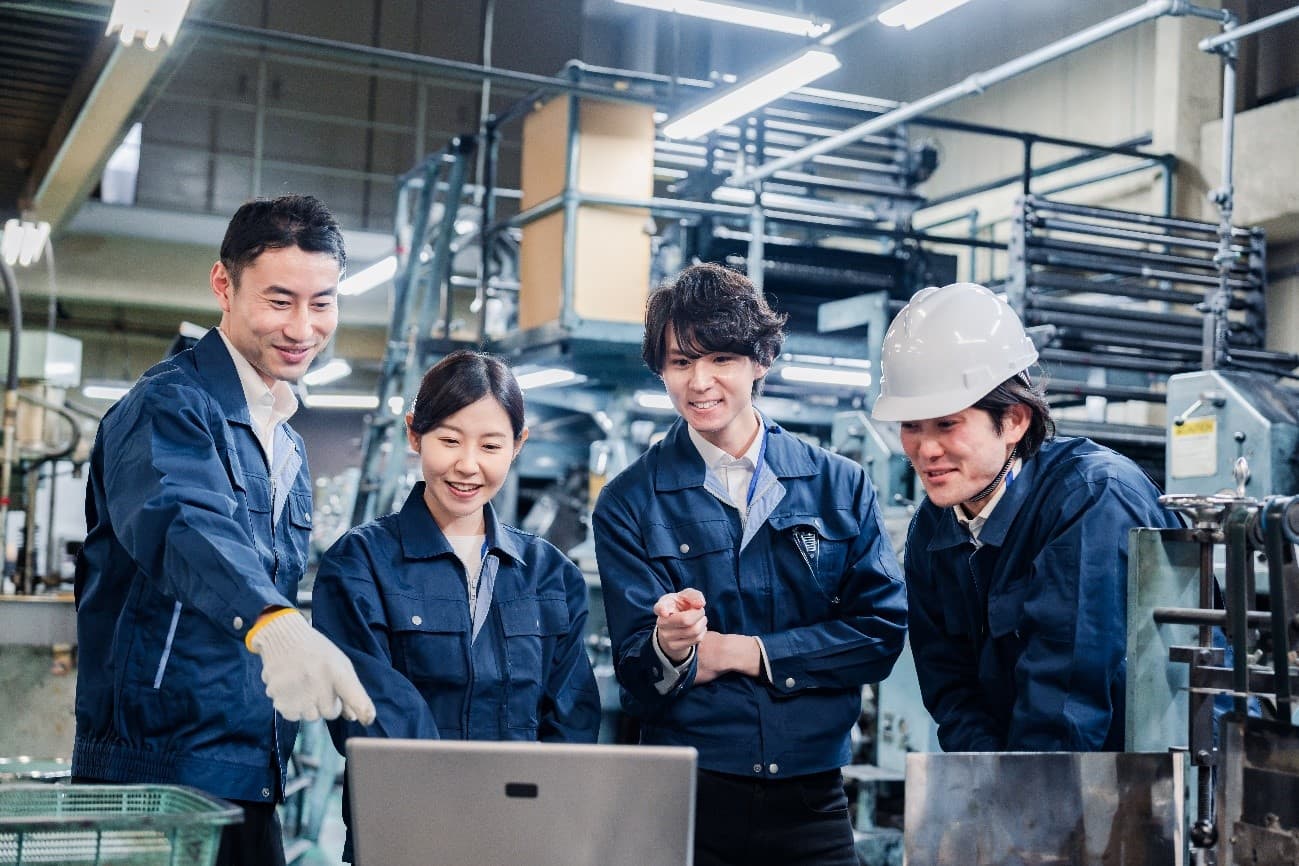
2024.04.15
工場の業務効率化を進める方法とは?印字の自動化などアイデア10選
「工場・製造現場での作業を効率化したい。でも、どこから手を付ければいいのかわからない…」とお悩みではありませんか?
工場の人材不足が深刻化する中、少子高齢化による労働人口の減少、グローバル競争の激化などの事情もあり、「業務効率化による生産力の向上」は製造業が抱える大きなテーマの一つとなっています。
そこでこの記事では、工場の作業効率化を行うメリットと効率化に役立つアイデアをご紹介します。
すぐに取り入れやすいアイデアを多数ご紹介しますので、ぜひ参考にしてください。
工場を効率化すると得られるメリット
工場効率化の実現によって多くのメリットが得られます。ここでは主なものをご紹介します。
利益を増やせる
生産性を向上させて生産量が増えると、多くの製品を販売できるので利益が増えます。
コストを減らせる
作業の効率化を進めると、作業員を減らすことが可能になり、人件費などのコストを削減することができます。
新たな人員を確保しやすくなる
人手不足に陥っている製造業では、作業員一人あたりの負担が大きくなりがちです。そのために残業が増えるなどすると作業員のモチベーションが低下して離職しやすくなります。
作業を効率化することでワーク・ライフ・バランスが充実した職場になれば、作業員の職場への定着が期待できるほか、新たな人員も確保しやすくなります。
顧客満足度が向上する
効率化によってスピーディーに不備の少ない製品を製造できるようになれば、顧客満足度が向上します。顧客満足度が向上すれば売り上げもアップしていくでしょう。
工場の効率化・生産性向上に繋がるアイデア10選
製造業で生産性を向上させるために有効なアイデアをご紹介します。
無駄な作業を減らす
まずは業務の流れをすべて見える化し、そこから改善案を考えていきましょう。
無駄に時間がかかっている作業は改善し、不必要な作業は省きます。ちょっとした無駄な作業でも、何度も繰り返しているなら膨大な時間を浪費していることになります。そのため、ささいに思えることでも見逃さずに改善していくことが大切です。
一部の従業員に負担がかかりすぎないようにする
従業員の業務量を均等に分散することも大切です。一部の従業員に負担が集中すると、ミスを起こしやすくなり、生産性も低下します。さらに、従業員の不満が積み重なれば、離職率の上昇につながりかねません。
最適な設備レイアウトに改善する
生産性向上のために、生産ラインのレイアウトを最適化させることは非常に重要です。作業工程や従業員の動線を考慮し、最適なレイアウトを検討しましょう。これにより、移動や運搬にかかる時間を短縮し、加工、組み立て、検査の工程をスムーズに進行させることができます。
ベテランのノウハウを共有する
工場では、ベテランの従業員が長年の経験で得た知識やコツを活かして作業を行っていることが多々あります。この場合、ベテランの従業員が不在の時にミスや作業の滞りが発生する可能性が高まります。
これを防ぐためには誰もが同じレベルのパフォーマンスを発揮できるように、ベテランのノウハウを全従業員にしっかりと伝えることが必要です。口頭での情報伝達だけでは、聞き違いや情報の漏れなどが発生する可能性があるため、作業のコツやよくある質問への回答をマニュアル化しておくと良いでしょう。
特に細かい作業に関しては、チェックシートを作成し、それを見ながら作業するのが業務の効率化に効果的です。必要な情報や手順をマニュアルとして整備し、全ての従業員にその内容を読むよう促すことで、教育時間の短縮も実現できます。
部門間の連携がとれる仕組みを作る
各部門間で連携がとれていないとミスや無駄が生じがちなので、コミュニケーションをスムーズにとれる仕組みを作っておくと良いでしょう。工場が広い場合は無線を活用すると、いつでもスムーズに連絡をとることができます。
適切な在庫管理ができる体制を作る
製造業において在庫管理が適切でない場合、必要な部品の調達が遅れるなどして作業が滞ることがあります。一方で、過剰な在庫を抱え込まないようにも気を配る必要があります。
さまざまな工程をスムーズに進行させるためには、過不足のない在庫管理が必要不可欠です。
ミスを減らす仕組みや補助設備を導入する
作業ミスが頻繁に発生すると、業務の効率は大きく下がってしまいます。作業ミスの対策としては、若手の教育の強化、ミスを減らすための仕組みづくり、補助設備の導入、ミスの事例の情報共有と再発防止策の周知徹底などがあります。
作業ミスが続くと顧客からの信頼失墜や売り上げの減少に繋がる恐れがあるため、積極的な対策が必要です。
5Sを徹底する
製造業において、効率を高めるために有効な手法の一つが「5S」です。5Sは以下の5つの要素を指し、それぞれが重要な役割を果たします。
整理:必要なものと不要なものを整理し、不要なものを排除します。
整頓:ものを配置するルールを決め、すぐに取り出せるように整頓します。
清掃:定期的な清掃活動によって、ゴミや汚れを取り除きます。
清潔:整理・整頓・清掃を徹底して、常にきれいな状態を維持します。
しつけ:整理、整頓、清掃、清潔の原則を現場に浸透させるために教育を行います。
整頓では、物の収納場所をなるべく使う場所の近くに設置し、取り出しやすくすることが重要です。何がどこにあるか一目でわかるようにラベリングをするなどの工夫をすると、さらに取り出しやすくなるでしょう。
汚れは機械の故障の原因となるため、定期的な清掃を実施しましょう。また、現場が汚れにくい機械を導入すれば、清掃にかかる時間を削減することも可能です。
5Sを従業員に浸透させるためには、社内セミナーやトレーニングなどを通じて、従業員に周知し、実践してもらうことが重要です。従業員一人ひとりが整理・整頓・清掃を実践しなければ、すぐに散らかったり汚れたりして作業環境が悪化します。全従業員が5Sを徹底できるようになるまで、繰り返し教育を行いましょう。
トレーサビリティを導入する
トレーサビリティとは、英語の「Trace(追跡)」と「Ability(能力)」を結び付けた言葉です。製造や加工のプロセス、荷物の受発注などについて、追跡記録を取り、追跡可能な状態にすることを指します。トレーサビリティを実施し、そのデータを分析することで、生産や品質管理を効率的に行えるようになります。
業務の自動化を推進する
作業者が行っていた業務を機械に委ねる「工場の自動化」を行うことも効率化に有効です。機械は適切なメンテナンスを行えば長時間稼働できるため、生産効率が大幅に向上します。
工場の自動化には高額な設備投資、専門知識を持った人材、機械を設置する十分なスペースが必要になるケースが多いため、なかなか難しいと考える方も多いようです。しかし、高額な設備投資を必要としない自動化の方法も存在します。
例えば、製品への印字作業を考えてみましょう。
レーザーや産業用インクジェットプリンターを導入する際のコストは高額ですが、エアシリンダを備えたユニットにセットするだけで簡単に印字作業を自動化できるスタンプもあります。
このようなスタンプを選べば、高額な設備投資も専門知識を持った人材も必要なく、スペースの制約も少なくて済みます。さらに高性能のスタンプなら、文字かすれなどの印字トラブルのリスクも少なく、生産ロスを削減することができます。
あまり予算をかけなくても自動化できる作業はあります。現在行っている作業の中で、何か自動化できる作業はないか考えてみてはいかがでしょうか。
着手しやすい手作業から自動化の検討を
工場の業務効率化の取り組みを成功させるためには、小さな取り組みから始めるといいでしょう。まずは小さなスケールで変更を試み、その効果をしっかりと検証しましょう。このようにすれば、何か問題が生じた場合でも、すぐに対応できます。
本格的に効率化の取り組みを始める前に、変更が本当に効果的であるかどうかを確認するためのテストを行うことも大切です。また、導入によって新たな問題が生じないかも検討すべきです。特に、作業員に過度な負担がかからないか確認する必要があります。
工場の業務効率化には作業員たちの協力が欠かせません。作業員たちの協力を得るには、彼らが日々の作業で感じているストレスや不便なことについてヒアリングし、明らかになった問題を効率化によって改善すると良いでしょう。このようにすることで作業員のモチベーションも高まり、協力する意欲も増すはずです。
自動印字も可能!工場の業務効率化に役立つおすすめのスタンプ
シヤチハタでは工場での印字・マーキングに活用できる産業用スタンプを各種取り揃えています。簡単にきれいな連続印字が可能になるため、作業能率のアップが見込めます。工場の業務効率化をお考えの方は、ぜひご検討ください。
<おすすめのポイント>
連続印字可能回数約1,500回!インクの補充を頻繁にする必要なし
キャップなしでも乾燥しないため、キャップの取り外しも不要で効率的!
エアシリンダを備えたユニットにスタンプを取り付けると簡単に自動印字が可能!
印面が反転し、印字の度にインキを拾う方式なので、連続印字でも安定した印字品質を維持!
金属、プラスチック、ゴムなどの幅広い素材に簡単に印字可能
曲面や凹凸面にもきれいに印字できる
工場での印字・マーキングでは、対象素材や温度等の環境での使用する製品が異なるケースがあり、導入に向けてわからない点が多いことが障壁のひとつとなります。そんなときは、スタンプとインキで製品開発を続けるシヤチハタにご相談ください。まずはお問い合わせフォームからお困りごとをぜひ教えてください。

インキ
2024.04.10
【輸出メーカー必見】RoHS指令(ローズ指令)を解説!規制対象と求められる対応とは
EU圏内では、化学製品による人体・環境への悪影響の危険性から、特定の有害物質はRoHS指令(ローズ指令)によって使用が制限されています。日本国内では適用されないものの、輸出産業においては規制への対応が必要です。しかし、法改正により対象が10物質に拡大され、どこまで適用すべきか頭を抱えている企業の方も多いのではないでしょうか。
本コラムでは、RoHS指令とは何かについて詳しく解説いたします。RoHS指令の適用時に求められる対応もお伝えいたしますので、EUへの輸出製品を製造するメーカーの方はぜひご一読ください。
RoHS指令(ローズ指令)とは
まず、RoHS指令について、次の4点から理解を深めていきましょう。
RoHS指令の目的
改正RoHS指令(RoHS2)の内容
RoHS指令とWEEE指令の違い
RoHS指令とREACH規則の違い
RoHS指令の目的
「RoHS指令(ローズ指令)」とは、EUで定められた電気・電子機器の廃棄処理で特定有害物質を発生させる製品の使用を規制する法律です。英語での正式名称は「Restriction of the use of certain Hazardous Substances in electrical and electronic equipment」といいます。RoHS指令の目的は、主に次の2つです。
廃棄物処理の際に発生する有害物質から人体・環境を保護する
電気・電子機器をリサイクルしやすくする
ただし、RoHS指令は日本に適用される法律ではなく、国内での製造・販売においては各種環境および労働関連法に準じていれば問題ありません。
改正RoHS指令(RoHS2)の内容
法改正により、2019年7月22日から規制物質が追加され、制限・禁止の対象が6物質から10物質へ拡大されています。新たな指令は「RoHS2」と呼ばれ、施行後に旧指令は廃止されました。RoHS2では、以下が義務付けられています。
RoHSへの適合性の評価
RoHS対応製品へのCEマーキングの貼付
RoHS適合宣言書および証明書の作成と保管
適合宣言書や証明書には、メーカーと登録商標および識別情報を記載し該当製品へ添付するほか、製造元において10年間保存しなければなりません。
RoHS指令とWEEE指令の違い
「WEEE指令(ウィー指令)」とは、リサイクルにおける電気・電子機器の取り扱いを定める法律です。正式には英語で「Waste from Electrical and Electronic Equipment」といいます。RoHS指令が有害物質の使用を規制しているのに対し、WEEE指令では電気・電子機器の廃棄をリサイクルによって減らすことが目的です。
RoHS指令とREACH規則の違い
「REACH規則(リーチ規制)」とは、製品に含まれる化学物質のリスクを評価し、ECHA(欧州化学品庁)への登録を義務付けるルールを指します。英語による正式名称は「Registration, Evaluation, Authorization and Restriction of Chemicals」です。有害物質による被害を抑えることを目的としている点はRoHS指令と同じですが、REACH規制は含有自体を規制する内容ではありません。
RoHS指令(ローズ指令)の対象
RoHS指令の適用範囲について、以下3つに分けてお伝えいたします。
RoHS対象の10物質
RoHS指令の対象製品
RoHS指令の適用除外となる物質
RoHS対象の10物質
最新のRoSH2指令では、電気・電子機器における下記10物質の使用が制限されています。
カドミウム(Cd)
鉛(Pb)
水銀(Hg)
六価クロム(Cr+6)
ポリ臭化ビフェニル(PBB)
ポリ臭化ジフェニルエーテル(PBDE)
フタル酸ジエチルへキシル(DEHP)
フタル酸ジプチル(DBP)
フタル酸ブチルベンジル(BBP)
フタル酸ジイソプチル(DIBP)
上記の10物質には、最大許容濃度が設定されています。最大許容濃度は、カドミウムが0.01wt%、それ以外の物質は0.1wt%です。規定外の製品は、EU圏内で製造・販売できません。
RoHS指令の対象製品
RoHS2指令の対象となる電気・電子製品は、以下のとおりです。
大型・小型家庭用電化製品
情報・通信デバイス
民生機器(テレビ・ラジオなど)
照明
電動・電気工具
玩具・レジャー・スポーツ機器
医療用機器
監視・制御機器
自動販売機
上記に加え、RoHS2が発行した2019年からはAC1000V、DC1500V以下の定格電圧を持つすべての電気・電子機器が対象となっています。
RoHS指令の適用除外となる物質
RoHS2指令の附属書ⅢおよびⅣにより、以下の物質はルールの適用が除外されています。
真鍮内の鉛(4wt%以下)
はんだに含まれる鉛
蛍光灯の水銀
鋼材(鋼鉄)内の鉛(0.35wt%以内)
アルミ内の鉛(0.4wt%以内)
銅合金(真ちゅう)内の鉛(4wt%(40,000ppm)以内)
ただし、上記が適用除外となるのは技術的・科学的に代替が不可な用途のみです。さらに、除外期間にはそれぞれ期限があり、永久的ではありません。
EUに輸出する日本企業にはRoHS対応がどこまで求められる?
前述のとおり、日本ではRoHS指令を適用していないため、本来であれば必ずしも対応を要しません。しかし、EU向けの製品・部品を製造・販売するメーカーにおいては、RoHS指令への適合性の評価と宣言を実施し、証明書を作成しなければなりません。また、製品・部品がRoHS対象の物質を含まないかどうかの検査は、物質や含有量によって分析方法を変える必要があります。RoHSへの対応プロセスが煩雑になるため、第三者機関での検査がおすすめです。
なお、RoHS指令に準じていない製品の輸出が発覚した場合、「RAPEX(EU緊急警告システム)」により通知され、リコールの対象になります。違反の際は罰金が課せられるだけではなく、製品回収にもコストがかかるでしょう。また、企業としての信用低下も免れないため、EU向けの輸出製品を取り扱うメーカーは慎重に対応する必要があります。
RoHS指令(ローズ指令)にも対応するインキを選ぼう!
RoHS指令の適用は、今や世界基準となりつつあります。日本ではまだ適用が義務付けられていませんが、輸出産業においては対応が不可欠です。国内でもいずれRoHS指令適用の流れとなる可能性もあるため、早急な対応が求められるでしょう。
シヤチハタでは、マーキング・インキで日本中の産業を支えつつ、環境にも配慮した技術開発を進めています。産業用マーキングにおける主力商品である「TAT(タート)インキ」は、RoHS指令などをはじめとし、国内外の主要な化学物質規制への対応(※)も万全です。あらゆる産業に最適なインキを展開しているため、コンプライアンスを高めたい企業の方はぜひ導入をご検討ください。※シヤチハタ株式会社 分析センターは、国際規格「ISO/IEC 17025(試験所及び校正機関の能力に関する一般要求事項)」に基づく審査を受け、この規格に適合し、試験所としての技術能力を有していると認定されています。「TAT(タート)インキ」は分析センターでRoHS分析をおこない、規制濃度以下であることを確認済みです。
▶️シヤチハタ製品のRoHS対応に関するお問い合わせはこちら

インキ
2024.04.08
染料と顔料ではどっちのインキがいい?マーキングにおける違いと見分け方
インキには、油性と水性の違いがあることはご存知の方も多いと思います。しかし、インキはさらに着色料で顔料と染料に分かれており、それぞれ適した使用シーンが異なることをご存知でしょうか?
本コラムでは、産業マーキングにおける顔料と染料の違いや見分け方を解説いたします。マーキングする素材別にどちらがいいのかも解説いたしますので、インキの選択にお悩みの際はぜひ参考にしてください。
インキの顔料と染料の違い
産業マーキングには、油性インキを用いられることが一般的です。同じく、油性インキにも顔料・染料の2種類があり、それぞれ異なる性質を持っています。まず、顔料と染料の違いからみていきましょう。
顔料インキの特徴
顔料インキとは、粒子が大きく、水分に溶けない性質を持っている塗料を指します。不透明のため、非浸透面への印字でも発色が明瞭でくっきりと表示できる点が特徴です。耐水性や耐光性にも優れており、さまざまな環境下で鮮明な印字が求められるマーキングに最適だといえます。
染料インキの特徴
染料インキとは、粒子が細かい水溶性の塗料のことです。幅広い素材に対応する汎用性の高さと、乾きの早さが特徴であり、連続なつ印にも使えます。ただ、印字対象が暗色の場合は印字が透けて見づらくなりやすいため、明るい色のインキを使用するほうがいいでしょう。
顔料・染料の見分け方
顔料・染料を見分けるポイントは、以下の5つです。
染み込みやすさ
乾きやすさ
にじみやすさ
退色しやすさ
仕上がり
染み込みやすさ
顔料インキは印字対象に塗料が付着して発色するため、インキが表面にとどまり、内部に染み込みません。一方、染料インキは印字対象の内部に浸透するしくみになっており、印字する素材によっては裏まで染みる可能性があります。
乾きやすさ
油性インキの場合、顔料・染料ともに乾燥時間が早い傾向にあります。ただ、あえていえば染料インキのほうが乾くまでにある程度の時間が必要です。
にじみやすさ
顔料インキは、水濡れに強く、印刷後のにじみや色あせが少ない性質です。染料インキは水溶性のため、比較的にじみやすくなります。
退色しやすさ
顔料インキは耐光性に優れ、長期間にわたり色あせしにくいのが特徴です。染料インキは光に弱いことから、経年劣化による退色・変色が起こりやすいといえます。
仕上がり
顔料・染料の大きな違いは、仕上がりの光沢感に現れます。染料インキは非常に鮮やかに印刷できるため、光沢紙などツヤのある用紙に印刷すると容易に見分がつくでしょう。
産業マーキングにおける顔料と染料の使い分け
ここからは、次の6つのケースに分け、顔料・染料どちらのインキがマーキングに適しているのかを解説いたします。
布・革へのマーキング
段ボールへのマーキング
木材へのマーキング
プラスチック素材・フィルムへのマーキング
工業部品へのマーキング
長期的な使用を前提とした製品へのマーキング
布・革へのマーキング
浸透面である布や革への印字には、染料インキが最適です。印字対象へすばやく染み込み、鮮やかにマーキングできます。
段ボールへの印字
段ボール箱などへの印字には、染料インキを選びましょう。染料は紙素材への浸透が早く、乾燥時間も短くなります。
木材へのマーキング
木材には、染料インキを使うときれいに印字できます。素材自体が凸凹しているため、表面に色付けする顔料インクでは、うまく印字できないケースがあります。
プラスチックフィルム・樹脂へのマーキング
プラスチック製のポリ袋やフィルムなど、光沢のある素材にカラフルかつ鮮明に印字できるのは染料インキです。ただし、硬質な樹脂に印字する場合、染料インキだと経年劣化によるにじみが起こる可能性があるため、顔料のほうが適しています。
工業部品へのマーキング
自動車のパーツや電子基板など、非浸透面へのマーキングには顔料インキが推奨されます。また、熱や薬品などにさらされることを考慮すると、染料インキだとにじみが懸念される点も顔料インキをおすすめする理由の一つです。
長期的な使用を前提とした製品へのマーキング
保存性が高いのは、顔料インキです。染料インキは、経年劣化による色あせが危惧されるため、長期保存には適していません。
インキ選びのお悩みはシヤチハタが解決!
インキと一口にいっても、その性質はさまざまであり、対象物によって適した素材が異なります。産業マーキングのインキを選ぶ際は、顔料・染料を用途に応じて使い分けるとよいでしょう。
スタンプで商品展開を長年続けるシヤチハタでは、染料・顔料ともに優れた製品を開発しています。インキナビのページでなつ印対象の素材・色に応じて最適なインキを検索できるためので、インキの選択に迷った際に活用してみてください。もちろん、直接ご相談することも可能ですなので、ぜひお気軽にお問い合わせください。

2024.04.05
なぜ今「多品種少量生産」なのか?印字の効率改善の観点から簡単に解説
消費者ニーズの傾向が変化したことにより、現代の産業は多品種少量生産の時代です。しかし、柔軟な対応を優先すると生産効率が落ちてしまうことにお悩みの企業の方も多いのではないでしょうか?
本コラムでは、多品種少量生産の特徴と背景、メリットを解説いたします。多品種少量生産の課題である印字の効率化の方法もお伝えいたしますので、ぜひ参考にしてください。
多品種少量生産とは
まず、多品種少量生産について、以下3つの視点から理解を深めていきましょう。
多品種少量生産の特徴
多品種少量生産が注目される背景
多品種少量生産のニーズが高い業界と事例
多品種少量生産の特徴
多品種少量生産とは、同じ生産・加工場所で複数種類の製品を小ロットで製造することを指します。要するに、取り扱う製品のバリエーションを増やし、さまざまな製品の在庫を少しずつ抱えておく生産方式です。あらかじめ受けた注文をもとに製造を行う個別受注生産と組み合わせられることも多く、幅広いニーズに対応できるようになります。
多品種少量生産が注目される背景
現在の日本の企業では、個々の要望に応えることに重きを置く考え方が主流です。反対に「作れば売れる」という大量消費社会だった時代には、低コストで多くの製品を製造できる少品種大量生産が一般的でした。
少品種多量生産では同じ製品を大量に製造するため、需要の予測が立てやすく、高い生産効率とローコスト化を実現していました。しかし、時代の変遷とともに人々の価値観は一変し、消費者はそれぞれ自らの好みに合致した製品を求めるようになっています。少品種多量生産では細分化されたニーズに対応できないことから、多品種少量生産に方向転換する企業が増えました。
近年は、個別受注での大量生産を行うマスカスタマイゼーションにより、ニーズへの対応と生産効率の維持を両立するスタイルも普及しつつあります。
多品種少量生産が適した業界の例
多品種少量生産方式はあらゆる業界で採用されていますが、代表例として挙げられるのは食品やファッション関係など、個人の嗜好に差があるジャンルです。また、自動車や電子機器など、顧客の要望に応じたカスタマイズが必要な業界においても、多品種少量生産が適しているといえます。
多品種少量生産のメリット
少品種大量生産と比較した多品種少量生産のメリットは、以下のとおりです。
さまざまなニーズへ柔軟に対応できる
過剰な在庫を抱えるリスクが減る
さまざまなニーズへ柔軟に対応できる
同一商品を一律で生産するだけでは、細分化された現代のニーズに対応しきれないケースがあります。少品種多量生産で幅広い製品を製造すれば、柔軟な対応が実現し、顧客満足度が上昇するでしょう。流通量が少ないものの一定のニーズがあるニッチ市場にも参入できることから、新規顧客の獲得も期待できます。
過剰な在庫を抱えるリスクが減る
多品種少量生産では、大量の在庫を抱えておくことがほとんどありません。反対に、当初から多くの数を製造しておく少品種大量生産では、売り上げが思うように伸びなかった場合、廃棄処分する流れとなります。大量の廃棄はコストがかかるだけではなく、資源保全の観点からも問題です。多品種少量生産に切り替えることで、市場や消費者ニーズの動向に応じて生産・在庫を調整できるため、廃棄数が最小限です。
多品種少量生産の課題
多くのメリットがある一方で、多品種少量生産にはほかの生産方式と比べ以下のような課題解決が必要だといえます。
コストの増加
生産管理の煩雑化
コストの増加
受注に合わせて製造を行う多品種少量生産では、生産回数がおのずと増えることになり、そのぶんコストがかさみます。また、複数の原料・材料を少しずつ仕入れることになるため、大量仕入れによるコストダウン効果が得られません。仕様変更によるライン組み替えの際も、数が増えるとコストが大きくなりがちです。製品が違えば、製造・管理の方法も異なるため、各部門への人員配置により人件費もかかります。
生産管理の煩雑化
多品種少量生産では、それぞれ製造の方法や過程、納期が異なる製品を取り扱うため、一律で管理できません。受注に合わせて一から生産を始めると、納品までに時間がかかることから、生産性が上がりにくいのが難点です。
多品種少量生産を効率化する方法
多品種少量生産によるメリットを活かしながら、弱点である効率の悪さをカバーする方法として、下記3点が挙げられます。
受注頻度に応じて生産管理を最適化する
特定の製品の在庫を一定数確保しておく
段取り換えの回数・時間を削減する
受注頻度に応じて生産管理を最適化する
多品種少量生産では、いかに生産回数を減らせるかが効率化の鍵だといえます。受注内容を分析し、原価やコストを把握することで、最適な生産方法に近付けていくことが必要です。また、注文頻度の多いロットをパターン化し、その製造プロセスや人員の配置などを見直すことで、効率的な生産方法になるでしょう。
特定の製品の在庫を一定数確保しておく
多品種少量生産における生産効率をアップさせる方法として、ある程度の在庫を確保しておくことが挙げられます。あらかじめ注文・ニーズの多い製品の在庫があれば、受注状況に応じてスピーディーに対応できるためです。ただし、少品種大量生産と比べ、多品種少量生産ではニーズの把握が難しいため、予測を見誤ると多くの在庫を抱える羽目になりかねない点に注意してください。ベースパーツの在庫を確保しておき、受注内容に合わせてカスタマイズする方式なら、無駄が少なくなるのでおすすめです。
段取り替えしやすい設備・装置を導入する
製品の仕様に合わせて設備・装置を取り替えたり設定を変更したりするのは、非常に煩雑な作業であり、生産効率を下げる要因になりかねません。そこで、手軽に設置できる設備・装置を導入すれば、段取り替えの時間を短縮できるでしょう。
スタンプで多品種少量生産ラインのマーキングを効率化!
ニーズが多様化する現代においては、多品種少量生産によるきめ細やかな対応が求められています。ただ、多品種少量生産では、効率が悪くなりやすいことが弱点です。ある程度の在庫をあらかじめ確保しておくとともに、生産プロセスおよび各種設備の最適化を図り、ニーズへの柔軟な対応と効率化の双方を両立することが大切だといえます。
最も手軽に見直せる設備の一つとして、産業マーキング装置が挙げられます。印字の技術開発を進めるシヤチハタのスタンプは、多品種少量生産の現場におけるマーキングにピッタリです。生産ラインにおける効率化・ローコスト化に関するお悩み解決に最適な方法を提案いたしますので、ぜひ一度お問い合わせください。
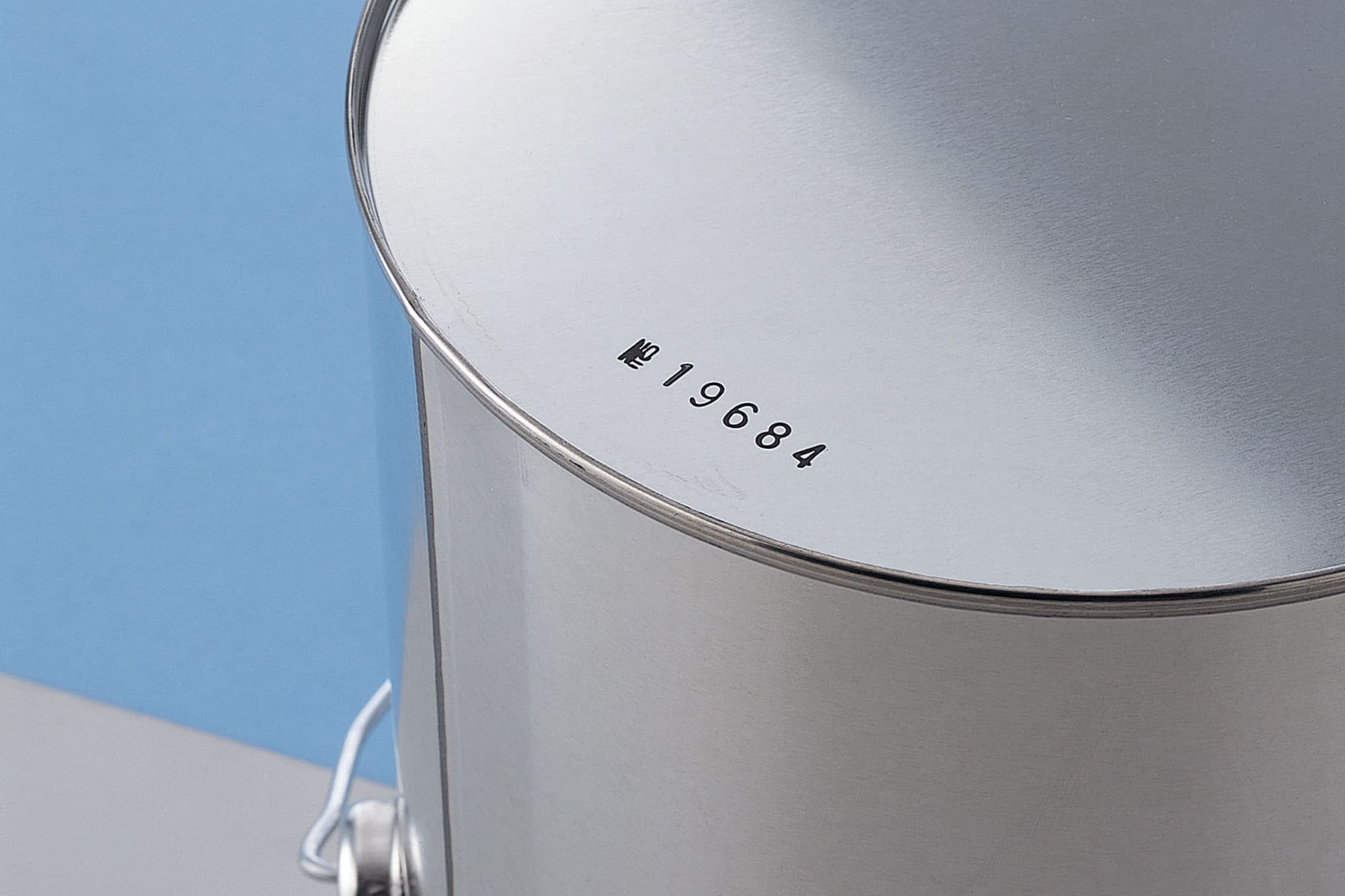
2024.04.03
金属(ステンレス・アルミ・鉄)にきれいに印字・マーキングする方法とは?
産業現場で頻用される金属素材ですが、マーキングをする際にインキを吸着しにくく、印字品質が保ちにくいこともあるのではないでしょうか?インキが付きにくい素材へのマーキングはいくつか注意すべきポイントがあります。
この記事では、金属印字に適したインクの選び方や金属印字の方法をわかりやすく解説します。ステンレス、鉄、アルミなどの金属製品に日付やロット番号、製造場所などの印字をしたいとお考えの方はぜひ参考にしてください。
金属への印字に適しているインキの特徴
金属にきれいに印字するには、まずインキ選びが重要となります。金属の印字に適したインキの特徴は以下の通りです。
速乾性がある
油性の溶剤が使用されている油性インキを使用することで、金属面への印字が可能になります。金属用のマーキングには速乾性が求められるケースが多く、1分以内など短時間で乾燥が必要になります。
速乾性のあるインキは金属のほかにもガラス、プラスチックなどの素材への印字に適しています。ただし、速乾性のある揮発性の高いインクは器具への固着(動作不良の原因になります)やインキかすれ(生産ロスに繋がります)が発生しやすいので、その点を対策してある製品と組み合わせて使う必要があります。
視認性が高い
黒など濃色の製品に印字する場合には、内容がはっきりと読み取れるように印字する必要があります。視認性が低いと画像検査装置が印字箇所を認識できない可能性もあるため注意が必要です。濃色の製品には白や黄色のインクで印字することで視認性を高めることが可能です。
耐熱性がある
金属への印字は製造工場などで使用されることが多いため、耐熱性も重要です。なつ印後に熱処理を行う場合は、処理後も高い視認性を維持できるインキを選択しましょう。
金属に印字する方法
次に金属に印字する方法について解説します。主な印字方法は3種類です。
レーザーマーカー
金属の表面を削って印字を行います。永久印字が実現できますが、削った箇所から腐食や錆が発生することがあるため、対策が必要です。
産業用インクジェットプリンタ
製品に直接インキを噴射するため、製品に傷をつけることなく印字することができます。永久印字はできません。
スタンプ(スタンパー)
導入費用やメンテナンス費用があまりかからないため、コストを抑えて印字することができます。導入が手軽で誰でもすぐ使えるというメリットもあります。
ハンディタイプのスタンプでの作業には人手が必要ですが、機械と組み合わせることで作業を自動化できるスタンプもあります。機能を絞れば低予算でも印字の自動化が可能です。
金属印字にスタンプ(スタンパー)を活用するメリット
大規模な工場で商品を大量生産する場合、通常はレーザーマーカーや産業用インクジェットプリンタを使用して印字されます。しかし、多品種少量生産の商品に印字する場合や小規模工場では、手軽に導入できるスタンプが適していることもあります。
金属印字にスタンプを活用するメリットは以下の通り。
コストがかからない
省スペース
メンテナンスが簡単
誰でも簡単に扱える
凹凸面への印字も可能
レーザーマーカーや産業用インクジェットプリンタは高機能ですが、導入やメンテナンスのコストが高額になりがちです。
そのため、印字の用途や予算に合わせて適切な印字機器を選ぶ必要があります。識別マークや日付などの単純な印字の場合、スタンプで十分です。スタンプは高機能な機器に比べてコストが低く、大幅に経費を削減できます。
金属印字用のスタンプ(スタンパー)を選ぶ際のポイント
金属印字にスタンプの導入を検討している方のために、金属印字に適したスタンプの特徴をまとめました。スタンプを選ぶ際に参考にしてください。
耐久性が高いスタンプを選ぶ
製造現場で金属面に印字する場合、スタンプには高い耐久性が必要です。おすすめは金属製のスタンプ。厳しい環境での連続印字に耐える強固さがあります。耐久性の高いスタンプを採用することで故障の頻度が下がるので、産業用に製造された頑丈なスタンプを選ぶといいでしょう。
安定性が高いスタンプを選ぶ
金属印字に適した速乾性のインキは、スタンプのゴムとパッド部の間に気密性がないとすぐに乾いてしまいます。インキが乾くと印字がかすれがちになり、生産ロスに繋がります。
ゴムとパッド部の間が密閉されているスタンパーを選び、安定して高品質な印字を連続で行えるようにするといいでしょう。
補充回数が少なく作業効率性が高いスタンプを選ぶ
1時間に1回など、インキの補充作業が頻繁に発生するスタンプでは稼働率が下がってしまいます。インキの補充回数が少なくて済むスタンプを選びましょう。
金属へのマーキングにはシヤチハタの強着インキでスタンプを
速乾性がある油性インキを選び、耐久性・安定性共に高いスタンプと組み合わせて使うと金属にきれいに印字することができます。また、濃色の製品に印字する場合は白や黄色などの視認性が高いインキ、なつ印後に熱処理を行う場合は耐熱性があるインキを選びましょう。 シヤチハタでは金属面の印字に適したインキとスタンプを取り扱っています。
さまざまな金属印字の用途に対応可能!シヤチハタのTATインキ
シヤチハタの「TAT(タート)」インキ(旧商品名:不滅インキ)は、揮発性のインキなので、速乾性が求められる金属への印字に適しています。TATインキの超微細粒子は金属などのインキを吸収しにくい素材にもしっかりときれいな印影を残すことができます。
速乾性や視認性など、金属印字に求められる用途は幅広いですが、TATインキなら豊富なラインナップから用途に合わせたインキを選ぶことができます。
インキカラーも豊富にご用意しているため、金属に高いコントラストで印字したいというニーズにも対応可能です。タイヤなどの濃色な素材への捺印が可能なスペシャルタイプ(受注生産インキ)もご用意。
また、TATインキはELV規制・RoHS指令等の国内外の法律で製造禁止、使用禁止の化学物質を使用していないため、安心してご使用いただけます。
TATインキでは、素材・対象物にあわせたインキを多数ご用意しているため、金属類以外にもさまざまな素材にきれいに印字することが可能です。TATインキで印字可能な素材は以下の通りです。
皮革類
木材
プラスチック類
ゴム
金属類(アルミニウム・鉄・ステンレス・真鍮・メッキ製品等)
塗装面
ガラス陶磁器
紙類
布類
このほか、特殊な素材に印字する場合や印影に二次加工を施す場合に適したスペシャルタイプのインキもございます。まずは一度ご相談ください。
金属にきれいに連続印字可能!シヤチハタのスタンプ
インキの付着が多すぎると文字がつぶれ、逆にインキの付着が少なすぎると文字がかすれるため、スタンプで安定してきれいな印字を続けることは難しいものです。
シヤチハタのスタンプは印面が反転し、その都度インキを拾う方式を採用。連続印字を行っても安定した印字品質を維持できます。印字待機時にはパッド部の気密性が確保される構造になっているため、長時間インキが乾くことがありません。さらにインキカートリッジを簡単に取り外してインキ補充ができるため製品が汚れにくくなっています。
シヤチハタのマーキング専用スタンプ「TAT金属印」は、金属だけでなくプラスチックやゴムなどの素材に簡単にマーキングできます。連続印字可能回数は約1,500回なので、インキの補充を頻繁にしなくても大丈夫です。
また、キャップなしでも乾燥しないため、キャップの取り外しも不要で、作業効率も非常に高いです。曲面や凹凸面にも印字でき、エアシリンダを備えたユニットにスタンプを取り付けると簡単に自動印字ができます。
シヤチハタのスタンパーは国内の自動車メーカーや大手部品メーカーで幅広く使用されており、金属印字のコスト削減や工数削減を求める方におすすめです。シヤチハタの技術が詰まったスタンプをぜひご検討ください。
金属への印字は、印字対象物の材質によって発色などが変わります。印字内容や印字対象物の素材、使用環境などをヒアリングして最適なインクとスタンパーをご提案させていただきます。まずはご相談ください。

スタンプ
2024.04.03
マーキング・印字の効率化はスタンプから!産業・工業の識別用を選ぶ際のポイントも解説
品質・サイズ表示や検品業務におけるマーキングに、どのような印字方式がいいかお悩みの方も多いのではないでしょうか?
手軽に作業を効率化したい場合、スタンプから検討を進めてみるとよいでしょう。本コラムでは、産業・工業の現場でスタンプを活用するメリットと、生産ラインに用いるスタンプの選び方を解説いたします。
マーキング・印字にスタンプを活用するメリット
マーキング・印字にスタンプ方式を採用する主なメリットを、以下5つの視点からみていきましょう。
誰でもすぐに使える
凹凸面にも印字できる
低コストで導入できる
スペースをとらない
簡単に修理できる
誰でもすぐに使える
スタンプは、扱いがシンプルです。ほかの印字方式と比べ複雑な操作がないため、誰でもすぐに使いこなせます。そのまま使う場合も、ユニット等でラインに組み込む場合も取り回しのしやすさが魅力の一つとなります。
凹凸面にも印字できる
マーキング用のスタンプの中には、平面だけではなく凹凸面にも対応可能なものがあります。レーザープリンタやインクジェットの中には凹凸にプリントできないものもあり、機器を使い分けることになればコストもかさむでしょう。スタンプであれば低コストで使い分けができ、識別印など印字内容によっては一つで対応可能な場合もあります。
低コストで導入できる
スタンプは、レーザーやインクジェットなどプリンタ式の印字機と比べ低コストで導入できます。メンテナンスもローコストであり、インキを補充すれば何度でも再利用できるため経済的です。
スペースをとらない
スタンプの設備は、極めてコンパクトな設計です。手動式なら一般的なハンコと同程度のサイズ感であり、ユニットを導入しても最小限のスペースで各種機械ラインに組み込めます。
簡単に修理できる
スタンプのメンテナンスは、インキカートリッジを取り外して交換するだけです。タート(TAT)溶剤による自主メンテナンスも簡単にできるため、ほかの印字方式と異なり、修理専門のサービスが必要になる機会はめったにありません。
マーキング・印字に最適なスタンプの選び方
産業の生産ラインにおけるマーキング・印字には、下記の条件を満たすスタンプがおすすめです。
耐久性がある
連続印字してもきれいに印字できる
インキ漏れ対策がなされている
耐久性がある
生産ラインでは、膨大な量の連続マーキングを行うケースがめずらしくありません。耐久性の低い機器を用いると、頻回のメンテナンス・入れ替えを要し、手間とコストがかかります。連続印字に耐えられるよう設計されたスタンプを選んでください。また、素材ごとにインキの吸収率が異なるため、用途に応じて使い分けることできれいな印影を長期間残せます。
連続印字してもきれいに印字できる
産業・工業に用いるスタンプは、安定した品質で連続印字できることが不可欠です。文字つぶれ・かすれなどの印字不良が頻発すると、その都度修正しなければならないため不要な手間がかかります。きれいに連続印字できるスタンプなら、作業時間の大幅な短縮が実現するでしょう。
インキ漏れ対策がなされている
印字機の液漏れは、作業を妨げる大きな要因です。また、スタンプを長期間利用しないとインキが詰まりやすくなりかねません。専用の溶剤などによるインキの不具合対策のほか、セルフメンテナンスでは問題が解消しなかった場合に丁寧なサポートが受けられる製品なら安心です。
【用途別】おすすめ製品6選
ここからは、産業・工業の現場で活用する用途別のスタンプ6種類をご紹介いたします。
タートスタンパー(浸透印)
タート回転スタンプ
タート回転ゴム印
リキッドスタンパーHD
TAT金属印
TATスタンプユニット
タートスタンパー(浸透印)
スタンプ台いらずで効率的になつ印できる、インキ内蔵式のスタンプです。角・丸型から、印面を自由にオーダーメイドできます。コマを差し替えることで日付を変更できる3サイズ展開の日付差替印もあるため、品番表示や検印など用途に応じて注文が可能です。
▶️タートスタンパー角型印の製品紹介はこちら
▶️タートスタンパー丸型印の製品紹介はこちら
▶️日付差替印の製品紹介はこちら
タート回転スタンプ
連続印字に最適なスタンプ台内蔵式の回転印です。強着性・耐水性に優れ、連続でなつ印しても印影のにじみ・かすみが起こりにくくなっています。また、購入後、インターネットや専用ハガキから印面が注文できるメールオーダーにも対応しています。
▶️タート回転スタンプの製品紹介はこちら
タート回転ゴム印
従来の回転式でありながら、特殊ゴム製の印字ベルトと文字表面に施した加工で滑りにくさ・捺しやすさを追求した工業用ゴム印です。長時間なつ印しても手が疲れづらいよう、ソフトなエラストマー素材のグリップで握りやすさにもこだわっています。欧文日付・和文日付・欧文6連の3種類の日付ベルトがあり、文字サイズも選択可能です。
▶️回転ゴム印タート用 欧文日付の製品紹介はこちら
▶️回転ゴム印タート用 和文日付の製品紹介はこちら
▶️回転ゴム印タート用 欧文6連の製品紹介はこちら
リキッドスタンパーHD
ペイントマーカーの代替として、濃色の素材に鮮明な連続なつ印ができるスタンプです。印面には柔らかいゴムを使用しているため、凹凸面・曲面の細かい溝にもインキがしっかりと入り込み、くっきりとマーキングできます。専用インキにはELV指令・RoHS指令をはじめとするさまざまな規制をクリアした安全性の高いものを採用しており、環境対応も万全です。
▶️リキッドスタンパーHDの製品紹介はこちら
TAT金属印
TAT金属印は、金属やプラスチック、ガラスなど、一般的なマーキングでは印字しにくい素材にもきれいな印影を残せるスタンプです。待機時は、パットが乾かないよう気密性が確保されています。捺すたびに印面が反転しインキを塗布する仕組みになっているため、連続なつ印しても品質が落ちにくいのも特徴です。各種産業機械に組み込んで自動印字ができる専用ユニットを活用すれば、工業の生産ラインにおけるマーキングの効率が劇的にアップします。
▶️TAT金属印の製品紹介はこちら
TATスタンプユニット
連続マーキングに対応した、タートスタンパー内蔵の自動なつ印機です。複動形エアシリンダが装備されており、操作はエアー供給の切り替えのみのため、手軽になつ印動作を制御できます。印面サイズは4機種から選択でき、オートスライドキャップで乾燥を防げる仕組みです。あらゆる機械に組み込みやすいコンパクト設計で、もちろん印字品質も良好。イニシャルコストを最小限に抑えて導入できます。
▶️TATスタンプユニットの製品紹介はこちら
印字・マーキングの効率化にはスタンプを!
扱いがシンプルなスタンプは、ほかの印字方式と比べて活用シーンが幅広いだけではなく、導入・運用も低コストです。産業・工業の生産ライン等に用いる際には、耐久性と印影の品質を維持できるのはもちろん、インキ漏れや乾き対策がなされているスタンプを選ぶことをおすすめします。
シヤチハタでは、産業分野を中心としたマーキング・印字に活用できるインキ・スタンプの技術開発を手がけてきました。使いやすさ・安全性・ローコストの3点が特長で、日本中のユーザーから選ばれています。お問い合わせフォームからスタンプオーダーもできますので、まずはお気軽にご相談ください。

インキ
2024.04.03
プラスチック・フィルムへ印字する方法とは?樹脂にも鮮やかに発色するインキもご紹介
樹脂製の容器やプラスチック・フィルムに印字したいけれど、最適な方法をお悩みの方も多いのではないでしょうか。結論として、鮮明かつ手軽に印字したいなら、スタンプ方式がおすすめです。
本コラムでは、樹脂製品・プラスチック・フィルムに印字できる4つの方法と、スタンプ方式を推奨する理由についてまとめました。あらゆる素材へ印字できるシヤチハタのインキについても解説していますので、ローコストで鮮明に印字する方法を知りたい方はぜひご一読ください。
樹脂・プラスチック・フィルムに美しく印字する方法
樹脂容器やプラスチック・フィルムなど、非吸着面へ鮮明に印字する方法は、次の4つが代表的です。
・シルク印刷
・産業用インクジェットプリンタ
・レーザーマーカー
・スタンプ
シルク印刷
シルク印刷とは、スクリーン版の上に載せたインキを対象物に押し付けて熱転写するタイプの印字方式です。プラスチックをはじめとする樹脂に鮮明な印字が可能であり、昔からその芸術性と耐久性の高さが注目されています。
ただ、シルク印刷は大量印刷に対応できる反面、少量だとコストが割高です。また、印字に欠かせない版板・版膜を作るコストも高く、カラー数を増やすほど経費がかさみます。さらに乾いて定着するまでに時間がかかる傾向にあり、生産ラインにおける識別マーキングなど、即座に印字する用途には使えません。
産業用インクジェットプリンタ
産業用インクジェットプリンタとは、工業や生産ラインにおけるプリント・マーキングに特化した印刷機です。設置型の設備のほか、手に持って使えるハンディタイプもあります。インキを粒状にして噴射する勢いで帯電させ、偏向電極によって曲げられた軌道に沿って印字面にプリントする仕組みです。
産業用インクジェットプリンタは、さまざまな素材および凹凸面にプリントできます。ただし、液漏れしやすく、にじみ・かすれの発生に気を付けなければなりません。また、設置型だと設備が大掛かりであり、持ち運びやちょっとした用途には向かないといえます。印字スタイルによって導入コストが数百万円にものぼることもあり、定期的なメンテナンス・インキ交換が必要でランニングコストもかさみがちです。
レーザーマーカー
レーザーマーカーとは、レーザー光を対象物に照射し、文字・数字を直に刻印する印字機です。樹脂・プラスチック・フィルムに使用するレーザーマーカーは、主に下記2つの印字スタイルがあります。
照射先を発泡させて白い刻印を浮かび上がらせるタイプ
対象物の化学変化を利用して印字するタイプ
レーザーマーカーによる印字は消えたりにじんだりすることがなく、印字速度が速いのが特徴です。しかし、材質ごとに仕上がりが異なり、相性が悪いとひび割れや視認性の悪化が生じるリスクがあります。また、イニシャルコストが非常に高く、操作スキルを要するため汎用性が高いとはいえません。
スタンプ
スタンプの印字機は、ほかの印字方式と比べ圧倒的なローコストが魅力です。スタンプの制作費用は1つ数千円から高くても数万円程度、メンテナンス用品や専用インキも安価で揃います。ハンディ・ユニットともにコンパクトなサイズ感のため、さまざまな場所へ持ち込みやすいでしょう。
なお、費用が安いといっても、印字性能が著しく劣ることはありません。凹凸面への印字が可能にもかかわらず、複雑な操作が一切なく、ハンコ同様にポンっと押すだけのため手軽に導入可能です。インキ内蔵型の浸透印を導入すれば連続印字にも対応できるうえ、インキを使い分けることであらゆる素材に印字できる汎用性の高さを誇ります。
樹脂・プラスチック・フィルムへの印字用インキにシヤチハタのタート(TAT)を使うメリット
コストを抑えつつ、業務効率アップが見込めるスタンプでの印字ですが、その性能は使用するインキによって大きく左右されます。樹脂やプラスチック・フィルムなど非吸収面への印字には、シヤチハタのタート(TAT)が最適です。ここでは、シヤチハタのインキが持つ下記3つのメリットをご紹介いたします。
印字が落ちにくい
高コントラストで印字できる
印字する対象物に応じてインキが選べる
印字が落ちにくい
シヤチハタのタートにはさまざまな種類があり、樹脂への印字に特化したタイプも展開されています。非吸収面にも鮮明に発色し、乾燥後は印影が消える心配がありません。樹脂・セロハンフィルムのほか、発泡スチロールやゴムへの印字にも対応しており、製造業の現場で幅広く活用されています。
対象物の性質に応じてインキが選べる
密着性のよさや耐熱・耐水など、求められるインキの性能は印字する素材によってさまざまです。シヤチハタのインキは、多目的に活用できるよう、素材の性質に合わせて乾燥速度が異なるインキを提供しています。樹脂・プラスチック・フィルムには、速乾性もしくは中速乾性のインキが最適です。
▶️強着スタンプインキ タート〈多目的用〉の製品紹介はこちら
高コントラストで印字できる
シヤチハタでは、高コントラストのスペシャルインキも多数取り揃えています。鮮やかな発色でくっきりとマーキングできるため、黒いタイヤや濃色基板の識別などでも簡単に見分けられるでしょう。
▶️強着スタンプインキ タート〈スペシャルタイプ〉の製品紹介はこちら
プラスチックなどの樹脂・フィルムへきれいに印字したいなら専用インキがおすすめ!
プラスチックをはじめとする樹脂製品やセロハンなどのフィルムへの識別マーキングには、手軽かつローコストで活用できるスタンプが推奨されます。各種プリンタでも印字の効率化が図れますが、導入・運用に手間と費用がかかるため、ハードルが高いでしょう。
マーキングスタンプには、日本のさまざまな産業に採用されているシヤチハタのタート(TAT)インキがおすすめです。プラスチックなどの樹脂・フィルムへの印字に特化した各種インキを取り揃え、お問い合わせフォームからご相談から受け付けています。

2024.04.02
トレーサビリティとは?必要性・メリットや重要なポイントもわかりやすく解説
トレーサビリティは、これまで食品産業や計量・計測器業界をはじめ、製造業で代表的に活用されてきたシステムです。近年は製造業だけではなく、IT化が進む産業でも注目度が高まっていることをご存知ですか?
本コラムでは、2種類あるトレーサビリティについて、具体例を交えながらわかりやすく解説いたします。トレーサビリティシステムの必要性やメリットに加え、うまく機能させるために重要なポイントもご紹介いたしますので、ぜひ参考にしてください。
トレーサビリティとは
まず、以下3つの視点から「トレーサビリティ」とはどのようなものなのか迫っていきましょう。
トレーサビリティの意味
トレーサビリティ普及のきっかけとなった事例
トレーサビリティのしくみ
トレーサビリティの意味
トレーサビリティとは、簡単にいうと、製品の製造ルートを明らかにすることを指します。英語の「Trace(追跡)」と「Ability(能力)」を組み合わせて作られた用語です。原材料の産地や生産過程、製造日時・場所などの識別情報を印字し、履歴を追跡できるようにしておくことで、製品の安全性と品質を向上させる効果が見込めます。
トレーサビリティ普及のきっかけとなった事例
トレーサビリティは、2000年はじめに起きた「BSE(狂牛病)問題」によって注目され始めたことから、従来は食品製造業で導入されるケースが一般的でした。しかしITの発展にともない、不正・改ざん防止策として、トレーサビリティの重要性が今後ますます高まると考えられています。
トレーサビリティのしくみ
トレーサビリティは、情報をさかのぼる「トレースバック」と、後の工程を追跡する「トレースフォワード」という2つのしくみから成り立っています。具体例を挙げると、製品の不備がどの製造工程で発生したのかをたどり、原因究明をスムーズにするための機能がトレースバックです。対して、製品の不備が見つかった際、すみやかに回収し被害の拡大を食い止めるためにその流通経路を追跡することがトレースフォワードです。
トレーサビリティの種類
トレーサビリティは、次の2種類に分けられます。
チェーントレーサビリティ
内部トレーサビリティ
具体例も交え、それぞれの違いをみていきましょう。
チェーントレーサビリティ
チェーントレーサビリティとは、材料調達・製造から消費者の手に渡るまでの全工程における物流を追跡可能にすることです。材料の入荷元へさかのぼったり、出荷先を追ったりなど、本来であれば自社の手が届かない範囲の工程を把握できるようになります。
内部トレーサビリティ
内部トレーサビリティとは、特定の事業所および工程に限定したモノの流れを追跡できるようにすることです。具体的には、自社での生産・加工のプロセスおよび出荷先の特定までを指します。各工程における作業内容や、製品の情報が紐付けることで、品質が向上するだけではなく業務の見直しに活用するという使い方もできます。
トレーサビリティ管理が必要な理由
トレーサビリティが必要な理由は、管理体制が確立できていない場合、以下のような問題が起こりかねないためです。
トラブル対応が遅れる
経済的損失が生じる
信用を損なう
トラブル対応が遅れる
物流工程が特定できないと、トラブルが発生した際の対応が遅れる可能性が高いでしょう。原因を究明している間にも、被害はどんどん広がり続け、消費者の安全が脅かされ続けるおそれがあります。
経済的損失が生じる
原因を突き止めないことには、どの工程に問題があったのかわかりません。そのため、流通している全製品の回収・廃棄が必要なうえ、生産を一時ストップせざるをえないことから、トラブル対応にかかる経済的損失は甚大です。
信用を損なう
製造工程にトラブルが発生した場合、取引先や消費者の不信感を煽ることになるため、信頼性の低下は避けられないリスクだといえます。さらに、どの工程に原因があるのかわからず問題への対応が著しく遅れると、顧客からの信用を失うことになるでしょう。
トレーサビリティシステム導入のメリット
トレーサビリティシステムを導入する大きなメリットとして、下記4点が挙げられます。
リスク管理の強化
顧客満足度の向上
信頼感の醸成
リスク管理の強化
識別情報・記号を印字しておけば、トラブル発生時の原因究明が容易です。問題の原因がすみやかに把握できれば、当該製品の回収作業がスムーズに行えます。トラブル対応にかかる費用および生産停止期間も、最小限に抑えられるでしょう。
顧客満足度の向上
トレーサビリティシステムでは、顧客情報を付与することも可能です。蓄積された情報・履歴は、データとして活かせるため、さらに満足度の高いサービスを提供できるようになります。
信頼感の醸成
トレーサビリティによってリスク管理の方法を明らかにすることは、取引先にとっても有益な仕組みだといえます。手に取った商品のルーツがたどれるようになれば、安心して購入できるためです。トレーサビリティを確立することで、安心・安全な製品を提供する企業というイメージの定着が図れるでしょう。
トレーサビリティを機能させるためのポイント
トレーサビリティは、次の3点を確保してはじめて適切に機能するようになります。
各サプライヤーとの協力関係
情報の一元化
正確かつ鮮明にマーキングできる印字方式
関係者との協力関係
トレーサビリティシステムには、全工程における供給元や利害関係者との連携が必要です。考え方や認識にズレがあると、トレーサビリティがうまく機能しなくなるため、協力体制の構築が欠かせません。また、トレーサビリティ管理の負担が大きくなりすぎないよう、各現場に適した範囲で導入するほうがよいでしょう。
情報の一元化
各工程で情報管理がバラバラだと、認識の相違が生まれ、トレーサビリティの利点を活かせないおそれがあります。例えば、製造現場では業務効率化を重視した情報管理が行われるのに対し、消費者に近い工程だとリスクヘッジに重きが置かれがちです。ブロックチェーン技術などを用いて情報を一元管理し、物流の全工程において有益なシステムを確立することが大切だといえます。
手軽かつ正確にマーキングできる印字方式
操作が難しく、印字不良やミスが多発する印字方式では、トレーサビリティが機能しません。あらゆる素材に印字できて手入れも簡単なスタンプなら、初期導入がしやすく、生産ラインでのマーキングに関するトラブルも抑えて運用できるでしょう。
▶️「TAT金属印」の製品紹介はこちら
トレーサビリティは鮮明な印字があってこそ!
製品に対する安心・安全が重視される現代において、トレーサビリティの徹底は重要な課題となっていくでしょう。そして、トレーサビリティは、正確かつ鮮明な印字が大前提です。
シヤチハタは、スタンプインキ技術による産業マーキングの効率化・リスクマネジメントに役立つよう、技術開発を進めています。マーキングやインキに関するご相談を受け付けていますので、トレーサビリティを支える印字方式をお探しの方はぜひお問い合わせください。

2024.04.02
段ボールへの印字の必要性と方法|実は難関なマーキングが手軽になるダイレクト印字とは
段ボールになぜ印字が必要なのかを正しくご存知でしょうか?また、段ボールへのスムーズかつきれいな印字は難しく、手軽にできる方法をお探しの方も多いでしょう。
本コラムでは、段ボール製の外箱への印字の重要性と、ダイレクト印字をおすすめする理由を解説いたします。段ボールへのダイレクト印字におすすめなシヤチハタのスタンプもご紹介いたしますので、印字業務の効率化にお役立てください。
段ボールへの印字が重要な理由
段ボール・化粧箱など、外装への印字は、トレーサビリティの実現に欠かせない大事な要素です。なお、トレーサビリティとは、簡潔にいうと追跡可能な仕組みのことを指します。
段ボールなどの外箱に印字があれば、等級表示が一目でわかるため、配送ミスを防止できます。また、万が一トラブルが発生した場合にも、ロット番号・バーコードなどから流通経路が明確化・把握できるため迅速な対応が可能です。
段ボールに適した印字方法
硬く半耐水性の紙からできた段ボールへの印字は、実は容易ではありません。よく用いられる次の2つの印字方式から、段ボールの印字をスムーズにする方法を考えていきましょう。
ラベラー
ダイレクト印字
ラベラー
ラベラーとは、ラベルシールを貼り付けるための機械のことです。自分で手に持って使うハンディラベラーや、自動・半自動タイプで大量・連続での貼付に対応する設置型など、さまざまな種類があります。
ダイレクト印字
ダイレクト印字とは、段ボールや化粧箱に印影を直接打つことを指します。ラベラーや転写式のプリント方式とは異なり、印刷の工程がシンプルで扱いやすい点が特徴です。大きい文字やイラストなども印字できるため、外箱をディスプレイ代わりに活用できます。
【ラベラーVSダイレクト印字】プロがおすすめする段ボールへの印字方式は?
結論として、プロ目線でおすすめしたいのはダイレクト印字です。
ラベラーはただラベルを貼り付けているだけのため、剥がれた際の貼り直しミスや改ざんなどの不備・不正のリスクがあります。貼付するラベル代の購入費など、ランニングコストも大きな負担です。
対して、段ボールに直接情報を印字すれば、剥がれる心配がありません。必要に応じて印字すればよく、あらかじめ印刷された予備の段ボールの用意が不要になります。そのため、表示変更による資材廃棄がカットできるうえ、在庫管理の負担も最小限です。総合的にみて、印字作業・管理の効率化にはダイレクト印字を推奨いたします。
段ボール・化粧箱に適したダイレクト印字の種類
ダイレクト印字にもいくつか種類がありますが、段ボールへの印字のしやすさを考慮すると以下2つの方法が適しています。
インクジェットプリンタ
スタンプ
インクジェットプリンタ
インクジェットプリンタとは、粒状インキを対象物に吹き付けて印字するタイプの印刷機です。段ボールの外装への印字には、高解像度で文字サイズの大きなオンデマンド型の産業用インクジェットプリンタがよく用いられます。
インクジェットプリンタは、文字・数字などの情報を入力するだけで印字できるため、誰でも手軽に操作できる点がメリットです。しかし、大量の印字では便利なものの、準備が大掛かりになるためちょっとした用途には使いづらいでしょう。
また、設置には一定の広さが必要であり、狭い現場や入り組んだ環境などには適しません。導入の費用が高いうえ、定期的なメンテナンスが必要であり、ランニングコストがかさむ可能性にも注意してください。
スタンプ
スタンプは、オーソドックスな印字方式です。シンプルな使い方だからこその汎用性の高さを誇り、自由に持ち運んで必要なときにさっと使えます。インキ内蔵型の浸透印なら、使うたびにインキの補充がいらず、連続印字にも対応可能です。
大きさ・サイズも自由にオーダーメイドできるにもかかわらず、導入費用が安価で一度購入すればランニングコストやメンテナンスに費用がほとんどかかりません。インクジェットプリンタなどの大掛かりな機器の導入はハードルが高く感じられますが、スタンプなら気軽に取り入れられて多用途に使えます。
段ボール・化粧箱にもきれいに印字できるシヤチハタのスタンプ
段ボールへの印字は、物流の円滑化に不可欠です。印字方式には、ラベラーの欠点を補えるダイレクト印字をおすすめします。手軽かつローコストで印字業務の効率化を図りたいなら、まずはスタンプから取り入れてみてはいかがでしょうか。
シヤチハタのスタンプは、段ボールに連続印字してもきれいな印影が維持できる耐久性を誇ります。インキは乾きが速く、水に流れない油性染料です。印面の形状は角・丸型の2種類があるほか、豊富なサイズやカラー、フォントから自由に組み合わせてスタンプが作成できます。要望に合わせてオーダーもできますので、お問い合わせフォームからご相談ください。
▶️段ボールにくっきり捺せる等級表示印 特角50号Xスタンパーの製品紹介はこちら

2024.04.02
よくある印字ミス事例とは?発生によるリスクや防止策を解説!
産業の生産現場では、印字ミスがしばしば発生します。商品自体の機能を損なうわけではないケースもあるとはいえ、重大な問題に発展する可能性もあり、たかが印字ミスと侮ることはできません。
本コラムでは、印字ミスの事例と、トラブル発生によるリスクを解説いたします。印字ミスを防止する方法も現場のリアルにもとづいて紹介いたしますので、ぜひ参考にしてください。
よくある印字ミス事例3選
生産現場におけるマーキングで起こりやすい印字ミス事例として、主に次の3つが挙げられます。
押し間違い
装置の不具合
ゴミの混入
押し間違い
印字ミスの原因として最も多いのは、押し間違いなどの人為的ミスです。指示内容の誤認や不適切ななつ印方法、作業前の確認不足が主な原因であり、不注意によって品質に差が出てしまいます。特に、プリンターなどを用いたマーキングでは、手作業より操作プロセスが複雑なため、人為的ミスが起きがちです。
装置の不具合
ノズルの詰まりや印字面の摩耗・劣化などがあると、印字不良が起こりやすくなります。また、作業前のチェック不足および待機中の不適切な処置も、印字ミスの一因です。適切な印字環境を維持するためには、定期的なメンテナンスが欠かせません。
ゴミの混入
チリ・ホコリなどのゴミが印字面に付着すると、情報を正確に印字できなくなります。作業中のゴミの発生を抑えるのは困難のため、除塵対策を徹底するとともに、印字面のこまめなクリーニングが大切です。
印字ミスによるリスク
印字ミスが起こった場合、以下3つのリスクが生じます。
コスト増大
生産停止
信用低下
コスト増大
印字ミスが起こった場合、トラブル対応にコストがかかります。該当製品を回収し、ミス・誤植を修正しなければならないためです。手直しだけでは済まない場合、製品自体を廃棄することになり、ミスの規模によっては大きな損害を被る可能性があります。
生産停止
印字ミスが見つかった際は、当該製品の出荷を一定期間ストップせざるをえません。提供できない間に、競合他社への乗り換えが起こり、取引先を失うことになる可能性もあるでしょう。
信用低下
印字ミスが発覚すると、ブランドイメージに少なからず影響があり、製品の売り上げ低下を招くおそれがあります。いったん低下した信頼を取り戻すのは容易ではなく、長期的な赤字に悩まされかねないことも懸念事項です。
印字ミスの防止策
印字ミスを防ぐため、下記4つのアイデアを紹介いたします。
スタンパーを用いる
インキの飛び散りに注意する
気密性を確保する
自動印字機を導入する
スタンパーを用いる
レーザーやインクジェットプリンタなどの機械は、操作にテクニックが必要であり、慣れていないと失敗しやすいという欠点があります。対してスタンプ方式によるシンプルな印字は、誰でも簡単に扱えるため、ヒューマンエラーによる印字ミスを抑えやすいでしょう。
▶️「TAT金属印」の製品紹介はこちら
飛び散りにくいインキを使用する
インキが飛び散ると、装置にこびりついて不良を招きます。補充時に飛散しにくいインキを使用することで、装置の不具合による印字不良を防げるでしょう。産業マーキングに適した「シヤチハタ」の金属印のインキには、カートリッジ方式が採用されているため、飛び散り・固着がほとんど起こりません。
気密性を確保する
印字機の待機中は、ゴミの混入や印字面の乾燥を防ぐため、密閉できる環境を確保しなければなりません。シヤチハタの金属印は、反転式の印面構造により気密性が高いため、良好な印字品質を長期間保てます。
自動印字機を導入する
手押しの手間やヒューマンエラーを軽減したいなら、スタンプの自動印字機の導入をおすすめします。自動でスタンプをなつ印できる装置があれば、連続なつ印の際も印字品質の安定化が可能です。「シヤチハタ」の自動捺印機には複動形エアシリンダが搭載されており、制御が手軽にもかかわらず高品質な印字を維持できます。
▶️「TAT金属印ユニット」の製品紹介はこちら
印字ミス対応へ真剣に取り組むなら「シヤチハタ」へ!
マーキング作業は、ちょっとした不注意で印字ミスが起こります。余計なコストやブランドイメージの低下を防ぐためには、操作方法がシンプルで誰でも扱いやすいスタンプ式の印字方式が導入しやすくおすすめです。
スタンプとインキの研究開発を長年続けているシヤチハタは、ローコストでの印字ミス解消をサポートしています。マーキングの効率化・省力化に関するご相談も受け付けていますので、ぜひお気軽にお問い合わせください。
▶️「シヤチハタの産業用マーキング」についてのお問い合わせ・資料請求はこちら

2024.04.01
生産ラインにおける印字不良の種類とは?欠け・かすれの原因とミスの対策と対応
生産ラインにおいて欠かせない工程であるマーキング。しかし、ところどころ欠け・かすれなどの印字ミスが発生することに悩まされている方も多いのではないでしょうか。
本コラムでは、産業マーキングにおける印字不良の種類および原因と対策を紹介いたします。印字トラブルが発生したときに求められる対応についても、わかりやすくまとめました。生産現場での印字不良によるデメリットを最小限に抑えたい方は、ぜひご覧ください。
生産ラインにおいて起こりやすい印字不良の種類
生産ラインで起こりがちな印字不良として、主に次の3種類が挙げられます。
印字欠け
印字かすれ
印字ムラ
印字欠け
印字欠けとは、印字の一部が欠けている状態です。上下いずれかが欠けていたり、ところどころ表示されない部分があったりなど、さまざまな欠け方があります。情報を正確に読み取れなくなるため、印字欠けがあると、商品として不適切と言わざるをえません。
印字かすれ
印字かすれとは、印字の全体もしくは一部がかすれ、薄く表示されている状態です。目視では非常に読みづらくなってしまうため、表示を見誤るリスクが高まります。
印字ムラ
印字ムラとは、印字の濃度が不均一な状態です。シミがついたような濃淡が出てしまい、見た目に美しくないだけではなく、乾燥時間に差が出てしまいます。
欠け・かすれが起きる3つの原因と対策
スタンプ式の印字で起きやすい印字ミスである欠け・かすれは、以下3点が原因となって起こることが多い傾向です。
メンテナンス不足
印字環境の不備
人為的ミス
上記それぞれの詳細と、対策方法もあわせて紹介いたします。
メンテナンス不足
チリ・ホコリなど汚れが付着していると、正常に印字できません。定期的にクリーニングし、汚れを取り除くことで欠け・かすれなどの印字ミスを防げます。スタンプはメンテナンスやクリーニングも手軽なため、こまめに手入れしておきましょう。また、使用しないまま放置すると、インキが固まりやすくなってしまいます。待機中は気密性を確保し、乾燥させないことが大切です。
印字環境の不備
経年劣化により、摩耗・破損やスタンプ自体の印字面のズレなどが生じやすくなります。スタンプ式なら交換時のコストも最小限ですので、ある程度使用年数が長くなってきたら交換を検討してください。
人為的ミス
手押しスタンプは、押し方によっては印字ムラが起きるケースがあります。自動印字装置を導入すれば、エアシリンダでスタンプを安定させられるため、印字ムラを減らせるでしょう。なお、シヤチハタのスタンプユニットには複動形エアシリンダが標準装備されており、乾燥による印字ミスの心配がありません。
▶️TAT金属印ユニットの製品紹介はこちら
印字不良の発生時に求められるトラブル対応
印字不良が発覚した際は、トレーサビリティの確保のためにも、すみやかな対応が推奨されます。求められる適切な対応は、以下のとおりです。
商品の自主回収
お詫び文の掲載
商品のリコール
被害を最小限に抑えられるよう、印字不良・ミスがわかり次第すぐに回収しなければなりません。なお、食品関係など消費者の健康被害につながりかねないジャンルでの自主回収の際は、法律により、行政への報告書の提出がルールです。自主回収する場合には、該当商品の回収・交換にコストがかかります。回収した商品は廃棄するしかないため、大きな損失となってしまうでしょう。
お詫び文の掲載・送付
印字不良が発生した際は、ミスに関するお詫び文を顧客・消費者へ送付もしくは自社のWebサイトなどに掲載する必要があります。対応が不適切だと不信感を煽り、顧客を失いかねません。信用失墜やブランドに対する悪いイメージの定着を防ぐためには、真摯な対応と今後の姿勢を示すことが重要です。
印字不良を正す試みで世界中の産業を支援する「シヤチハタ」
生産現場の悩みの種「印字不良」。印字不良にはコスト面・信用面でさまざまなデメリットがあり、できる限り避けたいトラブルです。
シヤチハタでは、これまで培ってきた技術をもとに、印字不良が起きにくいスタンプを製造してきました。生産現場のリアルにもとづき、印字のローコスト化・効率化・省力化に関するご相談も受け付けています。難しいと思われるような印字のお悩みも、どうぞご相談ください。
▶️印字不良にも対応できる「シヤチハタの産業用マーキング」についてのお問い合わせ・資料請求はこちら

2024.04.01
ダイレクトパーツマーキングとは?自動車産業に適した印字方式と読み取り時の問題点
トレーサビリティが注目される現代において、マーキングの正確性が自動車産業の課題となっています。マーキングの工程を効率化したいものの、どのような印字方式を選ぶべきかお悩みの企業の方も多いのではないでしょうか。そこでおすすめしたいのが、耐久性・汎用性の高いダイレクトパーツマーキングです。
本コラムでは、ダイレクトパーツマーキングの重要性と自動車産業に適した手法を解説いたします。ダイレクトパーツマーキング導入によるメリットと読み取り時に問題となるポイントについても詳しくまとめました。ダイレクトパーツマーキングをローコストかつ手軽に導入する方法もお伝えしますので、ぜひ参考にしてください。
「ダイレクトパーツマーキング」とは
ダイレクトパーツマーキング(DPM)とは、識別番号や製造日などの情報を付与する際、ラベルを貼り付けるのではなく対象物へ直に印字することです。文字や数字、図形のほか、バーコード・QRコードなどの各種コードを用いてダイレクトパーツマーキングが施されます。
自動車産業に適したダイレクトパーツマーキングの印字方式
自動車産業においてよく採用されているダイレクトパーツマーキングの手法として、次の4種類があります。
レーザーマーカー
インクジェットプリンタ
刻印機
スタンプ
レーザーマーカー
レーザーマーカーとは、可視光線を当てた際に発生する化学反応を利用した印字機です。出力を調節できるようになっており、対象物の素材や用途、保存期間に応じて印字の深さを決められます。設定に合わせてレーザーが正確に照射されるため、精度の高い印字が可能です。
ただ、レーザーマーカーは非常に高価な機器であり、イニシャルコストが大きくなる傾向にあります。また、打刻機など印字を直に刻み込むタイプの印字機より彫りが浅く、表面処理のプロセスを繰り返すとマーキングが消えるおそれが否めません。さらに、高熱による悪影響が懸念されるため、使える素材が限定的です。非常にハイパワーで危険性も高く、高い操作技術が必要ですので、安全対策を徹底した運用が求められます。
インクジェットプリンタ
インクジェットプリンタとは、対象物へインキを吹き付けて印字する機器です。凹凸のある印面にも、スピーディーかつくっきりと印字できます。インクジェットプリンタは比較的設置しやすく、操作方法もレーザーなどより手軽です。
ただし、対象物に汚れが付着していると、インクジェットプリンタではきれいに印字できません。また、摩耗に弱く経年劣化により印字が薄れるおそれがあるため、長期的な使用が前提の製品・パーツには向かないという特徴があります。
刻印機
刻印機とは、対象物を直接打刻し、印字を刻み込む機器です。刻印の深さで調節した光の反射を利用し、情報を読み取るしくみになっています。コードを点で表現するドットピンマーキングも、刻印機の一種です。刻印機は印字機自体が安価であり、導入時のコストが抑えられます。
ただ、刻印機はイニシャルコストが低いものの、定期的なパーツの取り替えが必要なため、ランニングコストがかさみがちです。また、打刻機でコードをダイレクトパーツマーキングした場合、印字の形状と配置が特殊になる傾向にあり、通常の読み取り機では対応できません。薄い素材に使用すると、貫通して穴が開くおそれがある点にも注意してください。
スタンプ
トレーサビリティを高めたいものの、予算に余裕がない場合の手段として、スタンプによるダイレクトパーツマーキングが挙げられます。アナログな方法ですが、スタンプなら持ち運びにも便利であり、使いたいときにすぐマーキングできる手軽さが魅力です。
導入・運用もローコストのため、ほかの印字方式との併用の際も負担が最小限です。実際に、金属パーツの生産ラインにおける識別記号やチェック時の検印などのマーキングには、スタンプがよく用いられています。
自動車業界でのダイレクトパーツマーキング導入のメリット
自動車業界におけるダイレクトパーツマーキング導入で得られる大きなメリットは下記の2つです。
トレーサビリティが確保できる
小さな部品にも印字しやすい
トレーサビリティが確保できる
自動車の部品などにダイレクトパーツマーキングを施し、情報を読み取ることで、半永久的に製造・物流ルートを追跡することが可能です。製品のリコールの際にも容易に所在が明らかになるため、スピーディーな対応が実現します。また、対象物に印字を直接刻み込めば、改ざんのリスクも少なく、途中で追跡できなくなる心配がありません。トレーサビリティが確保できれば、顧客満足度も向上し、メーカーとしての信頼性が高まるでしょう。
小さな部品にも印字しやすい
二次元コードなどをダイレクトパーツマーキングすれば、狭いスペースに膨大な量の情報を印字できます。大きな製品はもちろん、小さな部品の狭い範囲にもピンポイントで容易にマーキングできる点もメリットの一つです。
ダイレクトパーツマーキングの読み取りで生じる問題
ラベルと比較したダイレクトパーツマーキングの欠点は、以下の3つです。
光の乱反射が起きることがある
印字コントラストが低くなる
印字品質の統一が難しい
光の反射が起きることがある
ダイレクトパーツマーキングは対象物に傷を付ける形になるため、スキャナーの光が乱反射しやすいという特性があります。ハレーションが起こると、読取機からは表面が白飛びして見えてしまい、表示印字が読み取れなくなりかねません。
印字コントラストが低くなる
レーザーマーカーや刻印機を用いたダイレクトパーツマーキングでは、対象の表面を物理的に削り取るしくみのため、印字のカラーが選べません。暗色や透明の素材への印字の場合、周辺とのコントラストが低くなり、読み取りづらくなってしまいます。
印字品質の統一が難しい
ダイレクトパーツマーキングでは、印字機の付属品の劣化や素材の性質・形状などに多少の差があるだけでも、印字の品質にばらつきが生じやすくなります。特に2次元コードの印字品質が不均一だと、正確な読み取りが極めて困難です。品質を統一するためには、印字機の定期的なメンテナンスおよび印字対象の加工が必要であり、手間とコストがかかります。
低コストのダイレクトパーツマーキングならスタンプがおすすめ!
ダイレクトパーツマーキングは、大小さまざまなパーツへの正確な印字と、リコール時の迅速な対応を可能にするトレーサビリティ向上の有効手段です。自動車産業の生産ラインにおける印字プロセスの効率化を図りたいメーカーにとって、ダイレクトパーツマーキングを導入しない手はありません。
しかし、ダイレクトパーツマーキングの印字機は、イニシャルコスト・ランニングコストがかさむのが難点です。また、操作には一定のスキルが求められ、慎重に扱わなければミスや印字不良が頻発してしまいます。
コストをかけずにトレーサビリティを確保したいなら、まずはスタンプによるダイレクトパーツマーキングを導入してみてはいかがでしょうか。「シヤチハタ」のスタンパーは、創業から約1世紀にわたり改善や改良が繰り返されてきたマーキングアイテムです。品質の高さ・使い勝手のよさ・ローコストが特長ですので、ぜひ一度お試しください。
▶️シヤチハタの産業用マーキング」についてのお問い合わせ・資料請求はこちら

インキ
2024.04.01
【産業用】ガラス・セラミックや基板へきれいに印字するには?適したインキの条件も解説
さまざまな産業の生産ラインで取り扱われる特殊素材への印字には、専用の印字機が必要です。しかし、きれいに印字するためには方式だけではなく、インキも最適なものを選ぶ必要があることをご存知ない方も多いのではないでしょうか?
本コラムでは、ガラス・セラミックや基盤など特殊な材質への印字方式と、適したインキの条件を解説いたします。シヤチハタの強着インキである「TAT(タート)」の特長についてもご紹介いたしますので、ぜひご一読ください。
ガラス・セラミックや基板に印字する方法
膨大な連続作業を行う産業の現場でガラス・セラミックや基板にマーキングする際は、作業の安定性と定着力の強さを重視して次の印字方式がよく用いられます。
レーザーマーカー
産業用インクジェットプリンタ
スタンプユニット
レーザーマーカー
レーザーマーカーとは、入力された文字・数字を熱や光で照射して印字する機械です。印面を直に刻印するため、インキいらずで鮮明な印字を保つことができます。
ただ、素材ごとに適したレーザーマーカーがそれぞれ異なる点に注意してください。ガラス・セラミックや基盤は硬いため、パワーが弱いとうまく刻印できないか、強すぎると素材の性質によってはひび割れたり素材が溶けてしまったりすることがあるためです。
また、基板にレーザープリンタを用いる際は、レジスト透過によるパターンへの悪影響を考慮すると、印字方式がCO2レーザーに限られます。複数の素材を扱う産業では、何種類もの高価なレーザーマーカーを揃えなければならないため、コストがかさみかねません。
産業用インクジェットプリンタ
インクジェットプリンタとは、粒状にしたインキを印面に吹き付けて印刷する印字方式です。一般的なインクジェットプリンタは主に紙用ですが、産業用はさまざまな素材への印字に対応できます。
インクジェットプリンタによる印字は、表面に施したプリントのため、経年劣化やインク漏れなどによるにじみ・かすれが生じやすいところが難点です。とはいえ、さまざまな素材・面の形状に印字でき、あらゆる産業のマーキング作業を安全に効率化できる高性能な印字方式だといえます。
また、設置・組み込みも比較的容易であり、手軽に導入できることも産業用インクジェットプリンタの特徴です。
スタンプユニット
レーザーマーカーや産業用インクジェットプリンタの導入がコスト面から進まない場合には、スタンプを活用したユニットから取り入れるのもよいでしょう。手作業の置き換えとして、ローコストで導入しながら効率化を進めることができます。
印字内容の都度変更が難しいためロット番号等の印字には向きませんが、検査印などであれば導入しやすい方式のひとつです。
ガラス・セラミックや基板に印字するインキの注意点
ガラス・セラミックや基板に印字するためのインキは、下記の2点に注意して選んでください。
用途により求められる性質が異なる
素材の色に応じてカラーを使い分ける
用途により求められる性質が異なる
産業用プリンタのインキは、さまざまな用途に使える多機能性が求められます。例えば、飲料瓶に多用されるガラス・セラミックには接着力が高く、結露・アルコールに触れても消えない耐久性が必要です。機械工業の生産ラインにおいては、高温にさらされる環境のため、耐油性・耐熱性が高くにじみにくいインキが適しています。また、基板への印字には、金属やプラスチック・樹脂など材質・製法ごとにインキを変えなければなりません。
素材の色に応じてカラーを使い分ける
黒い液体を入れる瓶や、濃色への印字の場合、視認性を高めるため黒以外の高コントラストインキが最適です。そのため、ガラス・セラミックや基板に印字するインキには、多彩なカラー展開だけではなく、発色のよさも欠かせません。
印字用インキの要件を網羅したシヤチハタのTAT(タート)シリーズ
さまざまな素材や条件での印字に対応したインキを取り揃える、シヤチハタの「TAT(タート)」シリーズ。ガラス・セラミックをはじめとする非吸着面や、デリケートかつ濃色な基板などにも活用できるオールラウンドタイプのインキシリーズです。インキ色も豊富であり、既製品にない色や二次加工用に使えるスペシャルタイプもご要望に応じてご提供いたしますす。
スタンプとインキを主力商品に、100年近く事業展開を続けるシヤチハタが研究開発を通じて発展させてきた技術を、ローコストで取り入れてみませんか?
▶️強着スタンプインキ タート〈多目的用〉の製品紹介はこちら
ガラス・セラミックや基板への印字は高性能なインキがキーポイント!
ガラス・セラミックや基板への印字には、適したインキの選定が欠かせません。印字方式は、レーザープリンタにインクジェットプリンタ、スタンプユニットと幅広く現場の状況に合わせて導入を進めていきましょう。
特殊材質への印字を可能にするため試行錯誤して開発した、シヤチハタの「TAT(タート)」インキ。まずはお問い合わせフォームから、ぜひお気軽にご相談ください。

2024.03.29
製造業で頻用される印字方式とは?種類と違いをわかりやすく解説
生産現場で活用される印字方式には、さまざまな種類があります。それぞれ特徴が異なるため、適材適所で使い分けることが大切です。本コラムでは、製造業で必須の知識となる印字方式の種類について、具体的な機材や違いを解説いたします。印字方式の選び方を知りたい方は、ぜひ参考にしてください。
印字方式の種類と違い
印字方式は、以下の5種類が代表的です。
スタンプ
刻印
熱転写
インクジェットプリンタ
ラベラー
スタンプ
スタンプによる印字は、手書きに次いでローコストに実施できる方式のひとつです。ゴム印とスタンプ台を使う方法と、インキ補充が不要な浸透印の2種類があります。ほかの印字方式と比べ、メンテナンスのしやすさも含めて導入しやすいのが特徴です。
また、スタンプはコンパクトな設計であり、必要なときに誰でもすぐ使える手軽さが魅力だといえます。連続印字や識別マーキングなど用途に応じて使い分けられ、手作業と比較すると圧倒的に効率的に作業できるため、省力化・省人化を図りたい際に便利です。
刻印
刻印方式の代表例は、下記2つです。
刻印機
レーザープリンタ
刻印機は、人の手で対象物に直接深掘りしつつ、ローラーに転写されたインキを印字します。印字部分に消えない凸凹ができるため、くっきりして見やすい文字になることが特徴です。
一方、レーザープリンタは、CO2レーザーを照射して文字・図を印字対象に直接焼き付けます。ただ、印字速度が遅く、素材によっては文字が読みづらくなるのが欠点です。
熱転写
次に挙げるような印字機器は、ペットボトルのフィルム印刷によく用いられる熱転写による印字方式です。
ホットプリンタ
サーマルプリンタ
ホットプリンタは、別名ドライプリンタとも呼ばれ、高音にした感熱性インクリボンを対象へ圧着させることで文字を転写する機械です。速乾性があり、印字の見た目も美しいため、ペットボトルのフィルム等によく用いられています。ただし、活字式のため、熱で印字対象にピンホールが開くおそれがある点に注意しましょう。
サーマルプリンタは、ヘッドの発熱を利用した印字方式です。インクリボンを加熱して印字する溶融型転写方式と昇華型熱転写方式のほか、サプライ上のサーマルコート層へ直に熱をかけて自己発色させるダイレクトサーマル方式があります。活字方式ではないためピンホールは開きませんが、経年劣化で熱転写した印字が薄れる点がデメリットです。
インクジェットプリンタ
インクジェットプリンタは、インキの粒子をノズルから噴射し、文字盤から入力したデータに細かな点として吹き付けることで印字する仕組みです。OA機器としてさまざまなシーンで活用されており、パソコン・スマートフォンなどと接続することで、日時の自動印字・内容変更などを柔軟に設定できます。
インクジェットプリンタは印字対象が平面でなくとも美しくカラフルに印字できますが、細かい印字には向いていません。また、インキ代などのコストがかかることや、印字できない素材があるところが難点です。
ラベラー
ラベラーとは、印字されたラベルを対象に貼り付ける機械です。手に持って使用するハンドラベラーもあり、スーパーやコンビニの商品のラベル貼りなど、日常生活の身近なところで活用されています。ただ、ラベラーは、対象物に直接印字できないため、シール等が貼り付かない素材には使えません。
世界中で活用されるシヤチハタのスタンプ印字技術
シヤチハタの産業用マーキング商品なら、スタンプとインキを主力商品に100年近く事業展開を続けるシヤチハタが研究開発を通じて発展させてきた技術をローコストで取り入れることができます。
さまざまな素材や条件での印字に対応するスタンプとインキを揃えており、ユニット形式でラインに組み込むこともできるため、まずはご相談から始めてみるのもよいでしょう。
「シヤチハタの産業用マーキング」についてのお問い合わせ・資料請求はこちらから
印字方式の違いを把握して最適な種類を選ぼう
印字には、方式によってさまざまな種類があります。それぞれ適した素材・使用シーンが異なるため、特徴の違いを正しく把握しましょう。
どの印字方式にするか迷ったら「シヤチハタ」のスタンプがおすすめです。ローコストによる印字の省力化・効率化の相談ができますので、どのようなお悩みもお気軽にお問い合わせください。
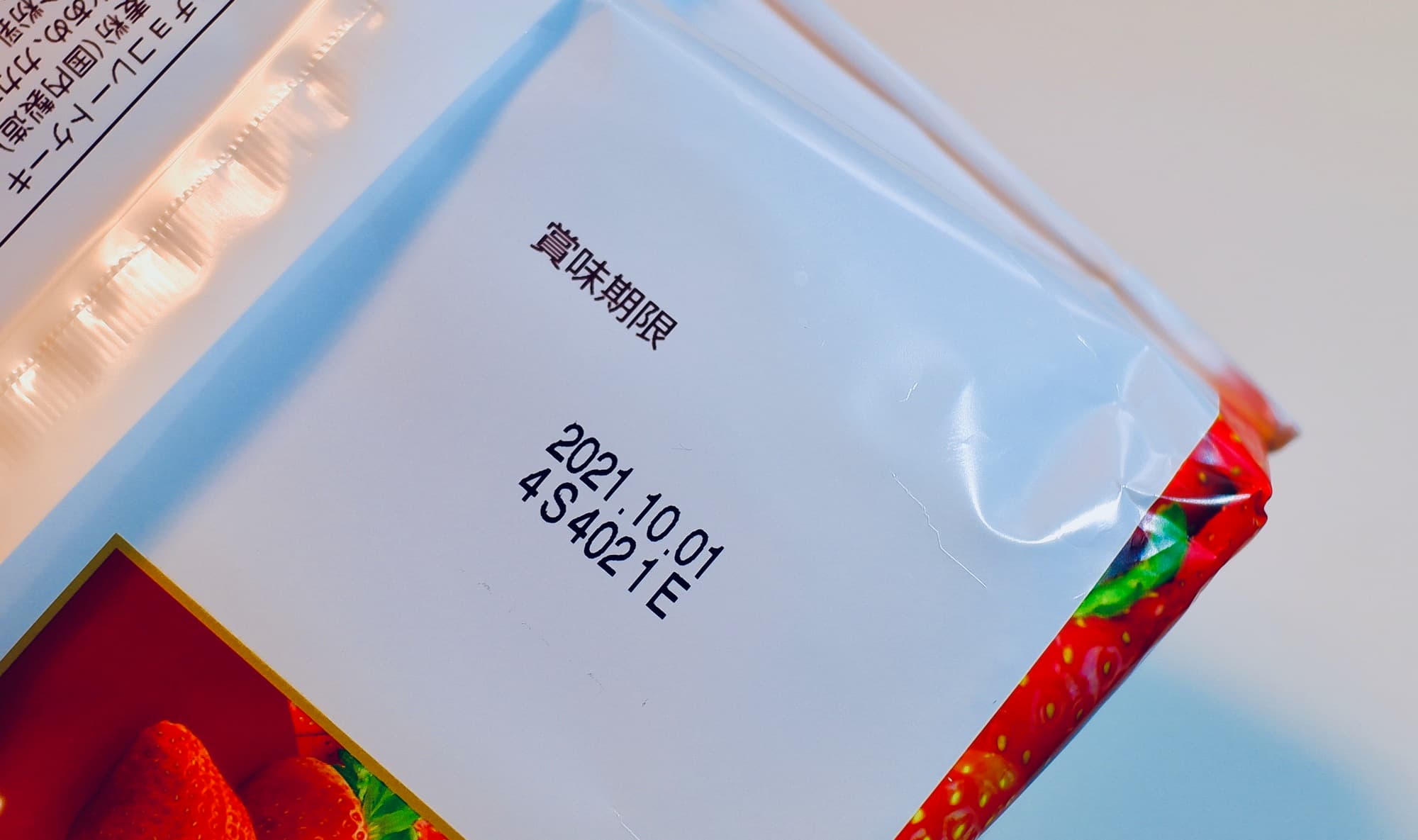
2024.03.29
印字とは?言葉の意味や生産現場におけるマーキングの目的・役割をわかりやすく解説
「印字」の正しい意味をご存知ですか?印刷・刻印との違いがわかりづらく、混同しているケースもあるかと思います。また、印字方式にはさまざまな種類があるため、方式別の適した使い方がご存知ない方も多いのではないでしょうか。
本コラムでは、印字の意味をふまえ、生産現場における目的・役割とは何かをわかりやすく解説いたします。マーキングが活用される身近な事例や工場での作業の流れもご紹介いたしますので、印字の基礎知識を身に付けたい方はぜひ参考にしてください。
印字(マーキング)とは?
まず、次の4項目から印字の概要を把握していきましょう。
印字の正しい意味と目的
印字と印刷の違い
印字と刻印の違い
印字作業に使われる機械の種類
印字の正しい意味と目的
「印字」という言葉は、本来の使い方では対象物に文字やマークを表示させること、もしくは印章そのものを指します。生産ラインにおける印字は、一般的にマーキングと呼ばれ、製品・部品への識別情報の付与を目的として実施されるプロセスです。適正に印字されていることで、トレーサビリティが実現し、モノの流れと安全性が確保できます。
▶️印字とトレーサビリティの関連性について詳しく知りたい方はこちら
印字と印刷の違い
端的にいうと「印字」は印刷の一種です。ただし、産業においては印字と印刷は区別される傾向にあります。印刷は、不変的な文字・図などを対象物に連続して写すことを表すケースが一般的です。対して印字は、同じ製品に製造番号や日付など場合によって変わる情報を付与する際に用いられるケースが多くなっています。
印字と刻印の違い
印字は、対象物へ情報・記号を付与する行為全般を表します。一方で刻印とは、対象物に直接刻み込むことで印字する方式のことです。つまり、刻印は印字の一種だといえます。
印字作業に使われる機械の種類
生産現場において、印字は下記のような印字機を使用して行われます。
スタンプ
刻印機
インクジェットプリンタ
レーザープリンタ
サーマルプリンタ
ラベラー
素材・用途ごとに適した印字方式が異なりますので、自社のニーズに合わせて印字機を比較しましょう。
▶️印字方式と選び方についてさらに詳しく知りたい方はこちら
身近な暮らしの中で活用されている印字
印字は、主に次のようなものに使われています。
食品の製造年月日や賞味・消費期限
化粧品の成分表示
薬品袋への名称表示
自動車の部品
電子精密機器の基板
上記のほかにも、印字の使い方はさまざまです。印字というと印刷や製造業以外には無関係のように思えますが、実は私たちの暮らしと密接に関わっています。
工場での印字作業の流れ
ここでは、工場における生産ラインでの印字(マーキング)に着目し、作業の流れをみていきましょう。印字は、以下のステップで行われます。
印字のレイアウトを設定する
テストを実施する
印字する
なお、操作や手入れ方法が複雑な印字機は、印字ミスや印字不良が起こりがちです。手軽に印字を導入したいなら、まずはスタンプ方式から取り入れてみてはいかがでしょうか。
印字のことならシヤチハタにおまかせ!
生産現場での印字(マーキング)とは、さまざまな製品への流動的な情報を表示させることを指します。印字は身近なシーンで活躍しており、トレーサビリティの維持・向上に欠かせない存在です。
シヤチハタは培ってきたスタンプとインキの技術をもとに、印字機器の導入による効率化・省力化を求める企業のニーズに応えています。スタンプでの印字なら、まずはご相談ください。
▶️シヤチハタの産業用マーキングについてのお問い合わせ・資料請求はこちらから
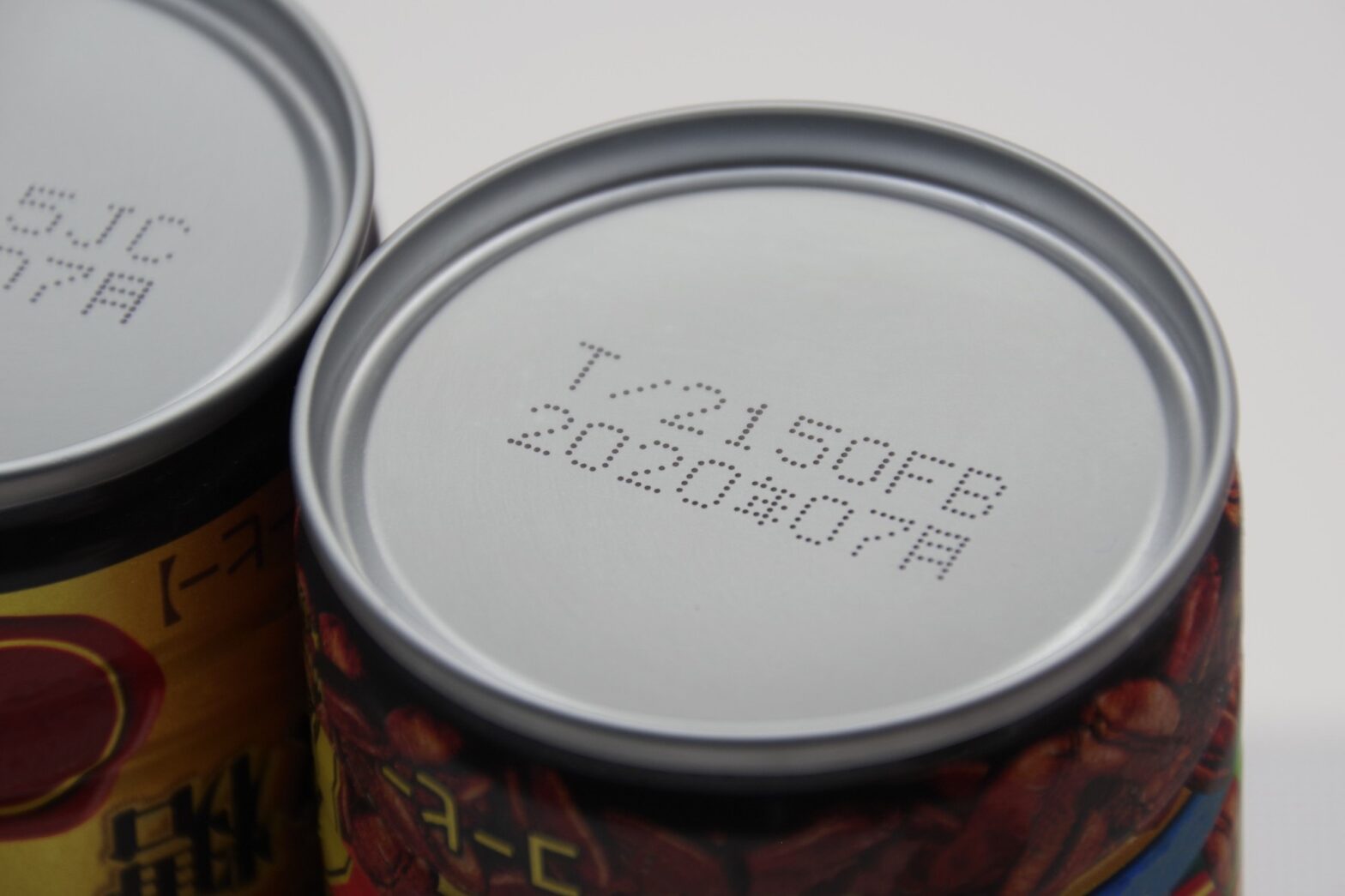
2024.03.29
ロットの意味とは?生産管理に役立つロット番号のメリットも解説
製造業などの現場では、「ロット」という言葉がたびたび用いられます。「ロット番号」といえば製品の生産・管理などをスムーズにするため活用されるものですが、「ロット」単体では使用されるシーンによって意味が変わることがあります。
今回は、ロットそのものの意味と使用されるシーン、活用することで得られるメリットのほか、さまざまな素材でできた製品へのロット番号印字に役立つアイテムをご紹介します。生産管理に関わる方は、ぜひご一読ください。
ロットとは使用シーンにおける"製品の最小単位"
生産などの現場で用いられる「ロット」とは、製品の単位として使用されるワードであり、「一定の数量をまとまりとした最小単位」を指します。ロットあたりの数量は、基本的に製品を提供する側が独自に設定可能なので、1ロットが10個の場合もあれば、100個の場合もあるのです。
仮に1ロット=100個だった場合、「1ロットから製造を請け負います」は「100個から製造を請け負います」という意味になります。つまり、この場合のロットは「製造を請け負う最低数を提示する単位」なのです。
1個単位ではなくロットを設定する理由は、コスト管理や効率化のためです。例えば、製品を1個つくるためだけに工場を稼働させると、時間もコストもかかりすぎてしまい、赤字になってしまうこともあるでしょう。
どれくらいの単位で製造すれば赤字にならないのか、採算がとれるのかを考えて生産するためには、ロットで注文を受ける必要があるのです。
使用シーン別で「ロット」が示す意味
ここでは、「ロット」という言葉が使用されるシーンによる意味の違いをご紹介していきます。
一回の稼働あたりの製造量を示す「製造ロット」
「製造ロット」は製品を造る際の最小単位を表しています。製造ロットを規定する理由は、在庫過多などによる損失やムダなコストを防ぐためです。製造の現場では需要や受注量などをみながら生産する量を調整しており、工場全体の稼働においても製造ロットの調整は重要な意味があります。
また、時期や場所などが同じ条件下で製造された製品に番号を振って生産管理を行なう方法は「ロット管理」と呼ばれています。
注文あたりに販売する製品数を示す「購入ロット」
製品を販売する際の最小単位を「購入ロット」と呼びます。販売側が購入ロットを決めているケースがほとんどですが、交渉によって数量と価格が調整されるケースも少なくありません。
注文を受ける最小数を示す「最小ロット」
「最小ロット」は受注の最小単位を表しており、製造側がきちんと利益を出すために設定されます。例えば、最低でも50個まとめて販売しなくては利益が得られない場合、最小ロットを50に定めることで、最低限の利益を確保することができます。
最小ロットも交渉が入るケースがあり、例えば、最小ロットは50個だけど30個だけほしいといわれることもあります。その場合、利益が出ないからと断ることもあれば、販売価格を引き上げて注文を受けることもあるでしょう。
ロット番号を使った生産管理のメリット
ロット管理は、製造業におけるスムーズな稼働に役立ちます。ここでは、ロット番号を使った管理のメリットについて解説します。
工程管理がしやすい
製品にロット番号を振り分ければ、製造から在庫管理、輸送、店舗での陳列・販売に至る一連の工程を一括管理することが可能です。どの製品が、どういった流れで出荷され、どの店舗に卸されたのかを調べられるので、発注のタイミングなども把握しやすくなります。
近年は、ロット管理技術の向上により一つひとつの製品にロット番号を付けられるようになったため、より質の高い管理システムを構築できるようになっています。
不良品を特定しやすい
不良品が発見されずに出荷されてしまった場合、大きな問題につながり、企業の信頼を損なってしまう事態を招きます。しかし、ロット番号で管理していれば、すぐに製造日が特定できるため、スピーディに不良品を回収できます。
トラブルに対して迅速に動くことができれば、影響を最小限に食い止めることが可能です。また、製品回収が効率よく進めば、その後のアフターフォローに時間を使うこともできるでしょう。
さまざまな素材を扱う製造現場のロット番号印字に
生産管理などに幅広く役立つロット番号ですが、製品の素材によっては番号の印字が難しいケースもあります。また、素材の違いでインキ定着具合に差があれば、品質の保証が難しくなってしまいますよね。
スタンプを長年扱うシヤチハタでは、独自のインキ技術をもとに金属やプラスチック、ガラス、ゴムなどにもインキを定着させることができる「タートシリーズ」を展開しています。
さらに、工場で大量の製品への印字が必要な場合には、生産ラインにエアー駆動式の自動印字機「タートスタンプユニット」を組み込むことも可能です。
印字の品質が安定しており、インキの成分も安全性を確保しています。低予算で導入できるほか、高さ20cmと場所を取らないコンパクト設計なのもうれしいポイントでしょう。エアー設備が整っていれば導入は難しくないため、生産現場でのマーキング作業のために自動印字機の導入を検討している方は、ぜひ候補に入れてみてはいかがでしょうか。
タートスタンプユニットについて詳しく知りたい方はこちら
ロット番号による管理で生産をスムーズに
今回は、製造現場で多用される「ロット」についてご紹介しました。製造や管理、販売を効率よくスムーズに行うためには、ロット番号による管理が便利です。効率化はもちろん、仮に不良品が出たときも番号によってすぐに対象製品の品番や製造日を特定でき、リスクも回避できます。
ロット管理を取り入れれば、製造業の業務効率をより高められるはず。ロット管理表を作成して在庫状況を可視化するなど、今一度方法を見直し、より効率的に生産できる環境を整えてみてはいかがでしょうか。